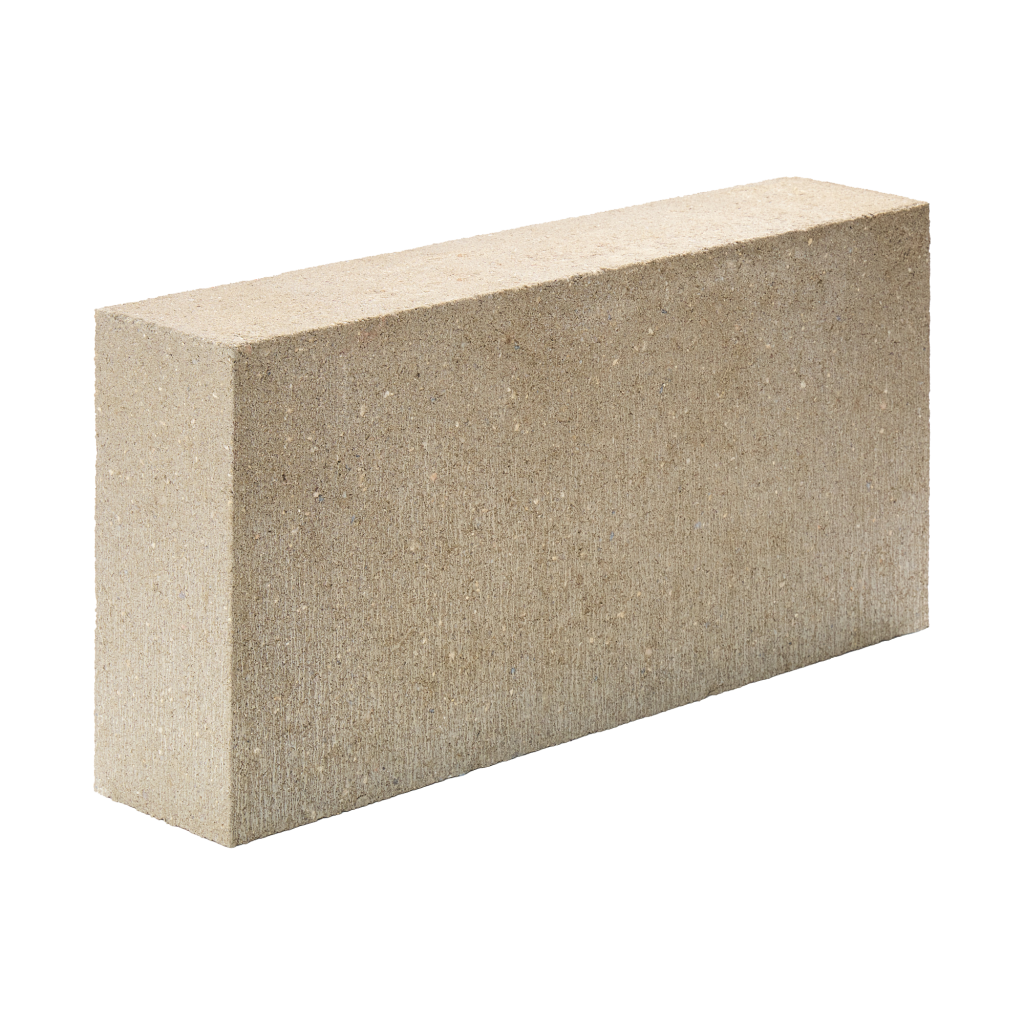
Lignacite ECO 70 Concrete Blocks
Lignacite ECO 70 concrete blocks are made with at least 70% recycled content. Not only does this conserve the use of primary materials, but it also results in a product with lower embodied carbon compared to most conventional masonry materials.
An independently verified Environmental Product Declaration (EPD) confirms the key environmental data of Lignacite ECO 70, ensuring transparency and sustainability.
Available in a Paint Grade finish, these blocks come in 100mm and 140mm thicknesses. The 140mm version is specially formulated to optimise block density with a unit weight of less than 20kg. This results in a slight colour difference to the 100mm block.
Lignacite ECO 70 blocks are robust and durable, offering excellent technical performance for a wide range of applications.
ECO 70 100 mm 7.3 N
ECO 70 140 mm 7.3 N
Block Gallery
Click an image to enlarge.
6 images
Block Benefits
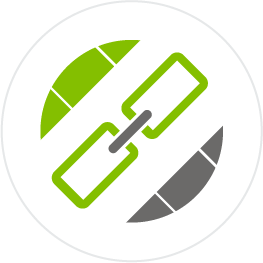
Durable
Suitable for use in academic, commercial and leisure buildings where durable and impact-resistant walls are needed.
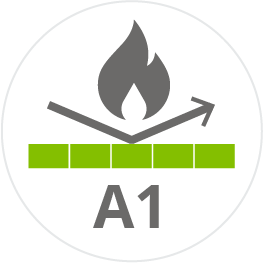
A1 Fire Rated
These non-combustible blocks make no contribution to fire, earning them a Class A1 rating.
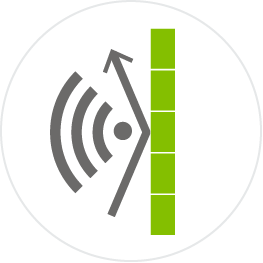
Excellent Sound Insulation
The relatively high mass and low porosity of Lignacite ECO 70 blocks results in outstanding acoustic performance. Walls built using 140mm Lignacite ECO 70 blocks can provide sound insulation up to 48dB (Rw)
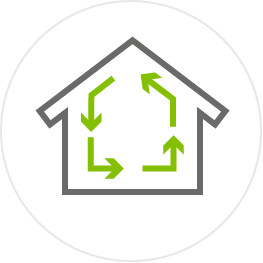
Air Tightness
Lignacite ECO 70 blocks have very low air permeability, especially when painted.
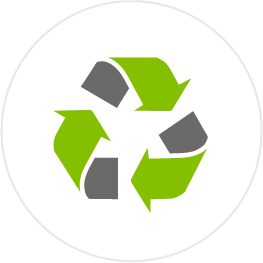
Recycled Content
Contains 70% recycled material, minimising the use of primary resources and helping protect the environment.
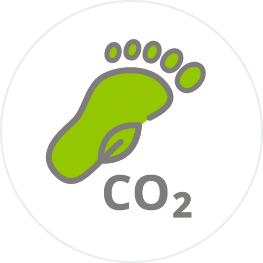
Carbon Savings
Delivers up to a 69% reduction in embodied carbon (A1–A4 stages) compared to Lignacite Standard medium dense blocks.
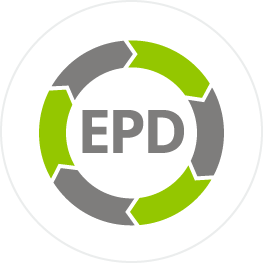
Independently Verified
Environmental Product Declarations (EPDs), certified by EPD Hub, confirm their sustainable credentials.
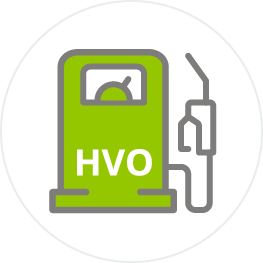
Low-Carbon Delivery
Opt for HVO-fuelled transport to lower delivery emissions by at least 90%.
Specification & Application
Block Standards
Lignacite ECO 70 blocks are BSI Kitemarked and certified to BS EN 771-3. They are also Category 1 masonry units manufactured under a BSI-certified Quality Management System, which is BS EN 9001 compliant.
Block Appearance
Lignacite ECO 70 blocks are medium-grey in colour with a close-textured surface making them suitable for direct painting. Where the appearance of the wall is important, it is recommended that a sample panel is constructed on-site to establish a benchmark for the standard of workmanship.
Block Application
Lignacite ECO 70 blocks are recommended for walls that are to be directly decorated. If left fair, some colour variation will be discernible.
Typical applications include:
- The inner leaves of external cavity walls
- Internal walls including fire break walls
- Separating walls
Where the appearance of the wall is important, walls of 210-215mm thickness are recommended to be constructed using two leaves of 100mm Lignacite ECO 70 blocks laid back-to-back and suitably tied. This construction is known as a collar-jointed wall.
Alternatively, if the appearance of the wall is not critical, a 215mm wall can be built using 100mm or 140mm Lignacite ECO 70 blocks laid flat.
Block Specification
Face Size | 440mm x 215mm |
---|---|
Thickness | 100mm, 140mm |
Mean Unit Strength | 3.6 N/mm², 7.3N/mm² |
Configuration | Group 1, solid blocks |
Dimensional Tolerances | Category D1 |
Net Dry Density | 100mm blocks - 1570 kg/m³.140mm blocks - 1450 kg/m³. |
Thermal Conductivity at 3% Moisture Content | 100mm blocks - 0.90 W/mK.140mm SP blocks - 0.79W/mK. |
Airtightness (m³/hr/m²)No finish | 100mm solid blocks: 5.5 |
Airtightness (m³/hr/m²)Paint one side | 100mm solid blocks: 0.6 (2 coats of emulsion paint) 5. |
Reaction to Fire | Class A1 |
Moisture Movement | <0.7mm/m |
Durability Against Freezing/Thawing | Frost resistance in accordance with PD 6697, Table 15. |
Weights & Pack Sizes
All weights are approximate and subject to normal variations in raw materials.
Table 1 – Block Weights and Pack Sizes
Size mm nominal (mm) (L x W x H) | Unit weight (kg) | Laid weight inc. mortar (kg/m²) | No. of blocks per pack |
---|---|---|---|
Solid 440 x 100 x 215 | 14.9 | 159 | 72 |
Solid 440 x 140 x 215 | 19.2 | 206 | 48 |
(1) Weights are based on 3% moisture content by weight.
Fire Resistance
Lignacite ECO 70 blocks are rated as Class A1 in accordance with BS EN 13501-1:2007+A1:2009. A1 materials are completely non-combustible and make no contribution to fire.
The fire resistance periods of Lignacite ECO 70 loadbearing and non-loadbearing walls are shown in Table 2, derived from the National Annex to BS EN 1996-1-2. This is applicable to all block strengths.
The fire resistance of loadbearing walls is influenced by the proportion of the load on a wall, which is annotated in the National Annex as a ≤1.0 or a ≤0.6. The fire values presented are based on the worst loading case (≤1.0) and can therefore be safely used for all loading conditions.
The thicknesses shown are for masonry alone, excluding finishes. For the fire resistance of walls with finishes, refer to the Lignacite Design Guide – Fire Resistance.
Table 2 – Fire Resistance
Block type (No finish) | Non-loadbearing wall (criteria E1) | Loadbearing wall (criteria RE1) |
---|---|---|
Lignacite ECO 70 - 100mm solid | 2 hours | 2 hours |
Lignacite ECO 70 - 140mm solid | 4 hours | 3 hours |
(1) Solid blocks are Group 1 units as defined in EN 1996-1-1
Sound Properties
Due to its relatively high mass and low porosity, Lignacite ECO 70 blockwork provides excellent levels of sound insulation between buildings and adjoining rooms. The Weighted Sound Reduction Index (Rw) values of various Lignacite ECO 70 wall constructions are shown in Table 3.
Table 3 – Sound Reduction Values
Weighted Sound Reduction Index: Rw, (dB):
No finish | Paint finish | |
---|---|---|
Lignacite ECO 70 - 100mm solid | 44 | 45 |
Lignacite ECO 70 - 140mm solid | 47 | 48 |
215mm solid (Lignacite ECO 70 - 100mm blocks laid flat) | 53 | 54 |
(1) Sound insulation values are based on technical assessments and tests to BS EN ISO 140-3.
(2) 215mm walls built using 100mm blocks laid flat cannot be regarded as a fair face wall. However, the construction will be suitable where the appearance of the wall is not important, or if the wall is to have applied finishes.
Thermal Properties
The thermal resistance values (m² K/W) for Lignacite ECO 70 blocks are shown in Table 5. The values are calculated by dividing the block thickness by its thermal conductivity (W/mK).
Table 5 – Thermal Resistance Values
Thermal Resistance (m² K/W): 3% m/c | |
---|---|
100mm Lignacite ECO 70 | 0.111 |
140mm Lignacite ECO 70 | 0.177 |
(1) 3% moisture content (m/c) should be used for protected locations, such as the inner leaf of external cavity walls.
The tables below show the U-values for a range of wall constructions based on 100mm Lignacite ECO 70 blocks with full and partial cavity insulation. The outer leaf is facing brick, but a rendered block outer leaf will usually achieve at least the same U-value. The U-values assume no surface finishes, other than paint.
Full Cavity Fill and 100mm Lignacite ECO 70 Blocks
Cavity fill type | No Finish U-values (W/m² K) |
---|---|
100mm DriTherm Cavity Slab 32 Ultimate | 0.28 |
125mm DriTherm Cavity Slab 32 Ultimate | 0.23 |
150mm DriTherm Cavity Slab 32 Ultimate | 0.20 |
100mm Isover CWS 32 | 0.28 |
125mm Isover CWS 32 | 0.23 |
150mm Isover CWS 32 | 0.20 |
90mm Kingspan Kooltherm K106 (plus a 10mm cavity) | 0.19 |
115mm Kingspan Kooltherm K106 (plus a 10mm cavity) | 0.15 |
140mm Kingspan Kooltherm K106 (plus a 10mm cavity) | 0.13 |
90mm Eurowall + (plus a 10mm cavity) | 0.21 |
115mm Eurowall + (plus a 10mm cavity) | 0.17 |
140mm Eurowall + (plus a 10mm cavity) | 0.14 |
100mm Xtratherm Cavity Therm | 0.20 |
125mm Xtratherm Cavity Therm | 0.16 |
150mm Xtratherm Cavity Therm | 0.14 |
Cavity fill type | No Finish U-values (W/m² K) |
---|---|
60mm Celotex CW4000 | 0.26 |
75mm Celotex CW4000 | 0.22 |
100mm Celotex CW4000 | 0.18 |
60mm Kingspan Kooltherm K108 | 0.24 |
75mm Kingspan Kooltherm K108 | 0.20 |
100mm Kingspan Kooltherm K108 | 0.16 |
60mm Eurowall Cavity | 0.26 |
75mm Eurowall Cavity | 0.22 |
100mm Eurowall Cavity | 0.18 |
100mm Rockwool Partial Fill | 0.28 |
150mm Rockwool Partial Fill | 0.20 |
170mm Rockwool Partial Fill | 0.18 |
100mm Isover CWS 32 | 0.27 |
125mm Isover CWS 32 | 0.22 |
150mm Isover CWS 32 | 0.19 |
(1) The U-values shown are based on the use of various proprietary insulation products. Alternative products can be used, provided they can achieve an equivalent thermal resistance (m² K/W).
(2) Wall ties are assumed to be stainless steel with a cross-sectional area of no more than 12.5mm² for structural cavities up to 125mm wide.
(3) The suitability of full fill cavity insulation materials will depend on exposure conditions and should be confirmed by the designer. For partial cavity fill, a 50mm residual should be maintained (always check the manufacturer’s guidance).
Sustainability
Block Environmental Management and Responsible Sourcing
Our manufacturing plants operate to a BSI-certified Environmental Management System (EMS), which complies with ISO 14001.
Lignacite Ltd also meets the requirements of BES 6001 – Framework Standard for the Responsible Sourcing of Construction Products (Certificate No: BES 580823). This independently awarded Responsible Sourcing Certification confirms that our products have been made with constituent materials that have been responsibly sourced. This extends to organisational governance, supply chain management and environmental and social aspects, all of which must be addressed in order to ensure the responsible sourcing of construction products. Certification to BES 6001 will allow credits to be gained under environment assessment schemes such as BREEAM.
Block Energy Management
A BSI-certified energy management system in accordance with ISO 50001 (Certificate No. ENMS 751020) is used to help manage energy use.
Compliance with ISO 50001 is a valuable tool in helping to manage energy use and includes the following outputs.
- A policy for more efficient use of energy
- Fix targets and objectives to meet the policy
- Use data to better understand and make decisions about energy use
- Measure the results
- Review how well the policy works, and
- Continually improve energy management
Block Recycled Materials
Lignacite ECO 70 blocks are manufactured with a minimum 70% recycled content.
Block Environmental Performance Declaration (EPD)
Key environmental performance data (in accordance with EN 15804+A2 and ISO 14025/ ISO 1930) can be found in the EPD for Lignacite ECO blocks.
Environmental Data Summary
A1-A3 (Production Stage) - 100mm Lignacite ECO 70 | 6.8 kg CO2e/m² |
---|---|
A1-A4 (Production & Transport) - 100mm Lignacite ECO 70 | 6.9 kg CO2e/m² |
A1-A3 (Production Stage) - 140mm Lignacite ECO 70 | 17.3 kg CO2e/m² |
A1-A4 (Production & Transport) - 140mm Lignacite ECO 70 | 17.4 kg CO2e/m² |
Table Note:
(1) A4 based on delivery into Central London using HVO fuel.
Source – Click here for all Lignacite ECO EPDs.
The Life Cycle Stage (A1-A3) refers to the extraction, processing, transportation and manufacture of materials and products up to the point where they leave the factory gate to be taken to site.
The notation ‘e’ is an abbreviation for tonnes of carbon dioxide equivalent.
Design
Block Structural Design
The design of walls using Lignacite ECO 70 concrete blocks should be in accordance with relevant design standards, including BS 8103: Part 2, BS EN 1996-1-1 and the requirements of the Building Regulations.
Block Movement Control
Vertical movement joints should be considered in accordance with masonry design codes and the recommendations of Published Document PD 6697, at 6.0 – 7.0 metre spacings. In areas of raised stress, such as above and below openings in external walls, the blockwork may need to be reinforced to restrain movement.
Block Service Life
When properly constructed, the durability of walls built using Lignacite ECO 70 products will match that of walls of traditional masonry and will fulfil their intended function for the life of the building in which they have been installed (typically 100 years). The concrete blocks themselves will require no maintenance.
Maintenance for walls will normally include the replacement of sealant in movement joints and at junctions/openings. Repointing for walls that are exposed to the elements may be necessary towards the end of their service life.
Block Wall Ties
Under normal conditions, wall ties should be embedded 50mm into the mortar on each leaf, staggered in alternate courses and spaced in accordance with the following.
Table 6 – Wall Tie Spacings
Leaf Thickness (mm) | Cavity Width (mm) | Horizontal Spacing (mm) | Vertical Spacing (mm) | Ties per m² |
---|---|---|---|---|
Less than 90mm | 50 - 75 | 450 | 450 | 4.9 |
Over 90mm | 50 - 150 | 900 | 450 | 2.5 |
Block Collar Jointed Walls
A 200-215mm collar-jointed wall can be built using two leaves of 100mm Lignacite ECO 70 blocks laid back-to-back and suitably tied. This construction is recommended for directly painted walls.
Walls can be tied together using metal ties or using masonry reinforcement e.g., AMR-CJ masonry reinforcement.
Design continued...
Block Mortar
Generally, the mortar type for work above ground level should be designation (iii) / Compressive Class M4. Stronger mixes may be required if blocks are used below ground.
Table 7 – Mortar Mixes
Mortar Designation (as per BS 5628-3) | Compressive Strength Class (as per BS EN 1996) | Recommended mix proportions of materials by volume |
---|---|---|
(iii) | M4 | 1:1:5 to 6 - Cement:Lime:Sand. 1:5 to 6 - Cement:Sand with or without air entrainment. 1:4 to 5 - Masonry Cement:Sand (with non-lime filler). 1:3½:4 - Masonry Cement:Sand (with lime filler). |
(ii) | M6 | 1:½:4-4½ - Cement:Lime: Sand. 1:3 to 4 - Cement:Sand with or without air entrainment. 1:2½:3½ - Masonry Cement:Sand (with non-lime filler). 1:3 - Masonry Cement:Sand (with lime filler). |
Site Practice
Block Surface Finish Recommendations
Direct Painting
A mist coat followed by at least two coats of emulsion will provide a good finish. The actual coverage will depend on the quality of the paint and how it is applied (e.g., brush, roller or by spray). Always ensure that each coat of paint has fully dried before any further layers are added.
Block Safe Handling
For detailed advice, refer to Lignacite’s Sitework Guide and the Material Safety Data sheet.
- Lignacite ECO 70 concrete block packs may be stacked on firm and level surfaces to a maximum height of 2 packs. Consideration of handling equipment’s suitability for site terrain and safety limits should also be given. Hand-operated pallet trucks may not be suitable unless pallets specific for this purpose are used and loads do not exceed the limits of the pallet truck or its operator(s). Care should be taken when opening packs that are wrapped or banded to ensure that items do not fall or otherwise endanger persons handling the blocks or those nearby.
- Handling of Lignacite ECO 70 concrete blocks should be undertaken in accordance with HSE Construction Sheet No. CIS77 ‘Preventing injury from handling heavy blocks’ (Construction Industry Advisory Committee) and in accordance with the Manual Handling Regulations 1992 (as amended). This concludes that there is a high risk of injury to individuals who repetitively manually handle blocks in excess of 20 kg. Where practical, mechanical handling equipment should be used to transport block packs to the area of work.
- Lignacite ECO 70 concrete blocks should not be installed if the temperature is at or below 3°C and falling. Lignacite ECO 70 concrete blocks should always be laid on a full bed of mortar and vertical joints solidly filled.
- For walls built undecorated, sample panels are recommended, which should be built prior to commencing Lignacite ECO 70 concrete block laying. This will serve as a benchmark for defining and specifying the quality of work required. Please note that block colour consistency is not guaranteed
- It is advisable to view sample panels at a distance of approximately 3m from the wall in good natural light.
Product Resources
Take a look at our handy downloadable guides, designed to help you get the best from our concrete blocks.
1 of 4