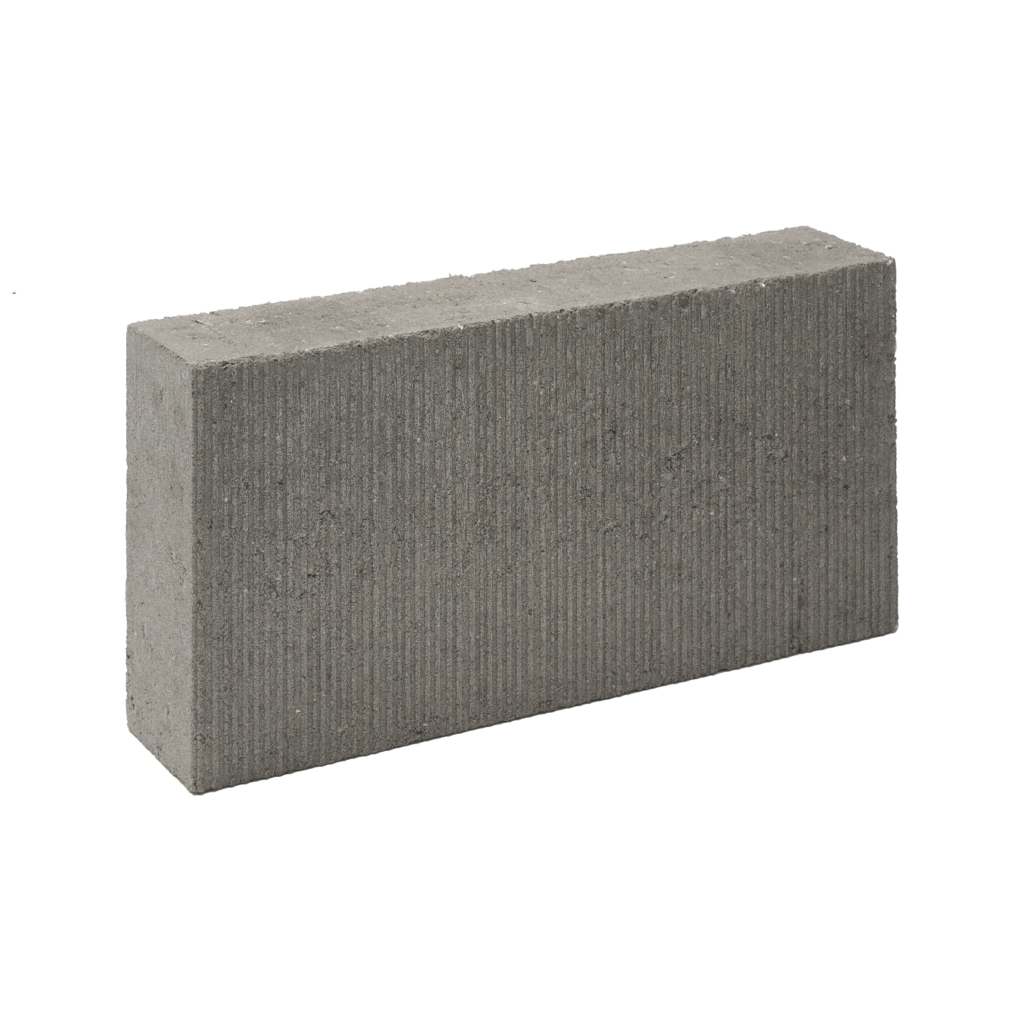
Lignacite GP Medium Dense Block
Lignacite General Purpose (GP) blocks are medium density and suitable for a wide range of applications above and below ground.
They are robust and durable and have a textured face, which provides an excellent surface for mortars, renders and plasters.
Manufactured to BS EN 771-3, Ligancite GP blocks contain a proportion of recycled materials, and their sustainability performance has been verified through an Environmental Performance Declaration (EPD).
Datasheet View our EPDsBlock Gallery
Click an image to enlarge.
6 images
Block Benefits
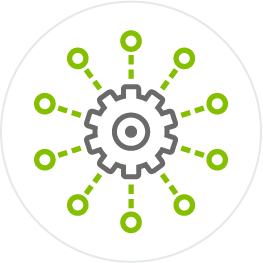
Universal Use
The Lignacite GP is an ideal block for constructing walls above and below ground, including external and separating walls. Its versatility also makes it a great choice as an infill block for beam and block flooring.
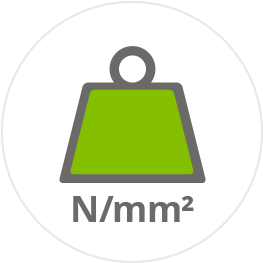
High Strength
With loadbearing strengths of up to10.4N/mm², these blocks are designed to cater for demanding loadbearing applications.
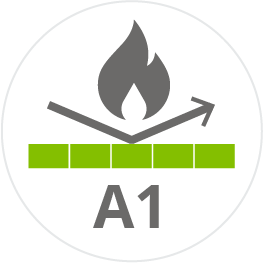
A1 Fire Rated
A Class A1 rating means these blocks are non-combustible and make no contribution to fire.
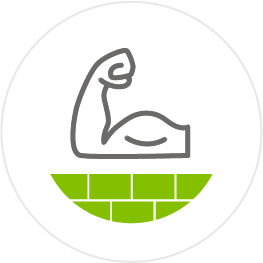
Strong Background
Lignacite GP blocks are ideal bases for plaster and render finishes and can support the weight of normal cladding treatments.
Specification & Application
Block Standards
Lignacite GP concrete blocks are BSI Kitemarked and certified to BS EN 771-3. They are also Category 1 masonry units manufactured under a BSI certified Quality Management System, which is BS EN 9001 compliant.
Block Appearance
Lignacite GP concrete blocks are manufactured with a distinctive scratched surface to aid the application of plaster and render finishes.
Block Application
Lignacite GP concrete blockwork suits all general-purpose walling applications. It is recommended that walls of 215mm thickness are constructed using 100mm blocks laid flat.
Typical locations include:
- The inner and outer leaves of external cavity walls
- Internal walls (including fire break walls)
- Separating walls (including those conforming to Robust Detail party wall specifications)
- Below ground (7.3N/mm² strength blocks should be used for walls that are exposed to the external ground)
- Infill units for beam and block flooring using 3.6N/mm² or 7.3N/mm² blocks*
*3.6N/mm² blocks have been transverse tested to ensure suitability.
Block Specification
Face Size | 440mm x 215mm |
---|---|
Thickness | 100mm, 140mm |
Mean Unit Strength | 3.6N/mm², 7.3N/mm², 10.4N/mm² |
Configuration | Group 1, solid blocks |
Dimensional Tolerances | Category D1 |
Net Dry Density | 1450 kg/m³ |
Thermal Conductivity | 0.47 W/mK at 3% moisture content (Internal use).0.51 W/mK at 5% moisture content (External use). |
Reaction to Fire | Class A1 |
Moisture Movement | <0.5mm/m |
Durability Against Freezing/Thawing | Frost resistance in accordance with PD 6697, Table 15. |
Weights & Pack Sizes
All weights are approximate and subject to normal variations in raw materials.
Table 1 – Block Weights and Pack Sizes
Face size (mm) | Thickness & block type | Unit weight (kg) | Laid weight inc. mortar (kg/m²) | No. of blocks per pack |
---|---|---|---|---|
440 x 215 | 100mm solid | 14.1 | 150 | 72 |
440 x 215 | 140mm solid | 19.7 | 211 | 48 |
(1) Weights are based on 3% moisture content by weight.
(2) The weights apply to all block strengths.
Coursing Blocks
Coursing Blocks compliment the use of standard size blocks. They can be used as infill as well as general coursing and their use will remove the need for on-site cutting, which reduces waste and improves productivity.
Their use will enable a uniform performance to be achieved throughout a wall.
Table 2 – Coursing Blocks – Weights and Pack Sizes
Face size | Thickness | Compressive strengths (N/mm²) | Typical unit weight (kg) | No. of Coursing units per pack |
---|---|---|---|---|
440 x 65mm | 100mm | 7.3, 10.4 | 4.2 | 208 |
440 x 65mm | 140mm | 7.3, 10.4 | 5.9 | 156 |
(1) To aid transportation, Coursing Blocks are supplied banded to pallets.
(2) Unit weights are approximate and based on 3% moisture content by weight.
Sound Properties
Lignacite GP concrete blockwork provides excellent levels of sound insulation between buildings and adjoining rooms. It can be used in cavity party wall constructions in dwellings, satisfying the specifications for lightweight blockwork in accordance with Building Regulations’ Approved Document E. It can also be used to construct party walls meeting Robust Detail specifications (e.g., Robust Details E-WM-2, 4, 14, 17, 20, 21, 22, 27, 28, 32, 33). The Weighted Sound Reduction Index (Rw) values of Lignacite GP wall constructions are shown in Table 3.
Table 3 – Sound Reduction Values
Weighted Sound Reduction Index: Rw, (dB):
Plaster finish | Plasterboard on dabs | |
---|---|---|
100mm Lignacite GP - All strengths | 45 | 44 |
140mm Lignacite GP - All strengths | 49 | 48 |
215mm Lignacite GP (100mm blocks laid flat) | 53 | 52 |
(1) Sound insulation values are based on technical assessments and tests to BS EN ISO 140-3.
(2) Surface finishes are assumed to be applied to both wall faces.
Fire Resistance
Lignacite GP concrete blocks are rated as Class A1, in accordance with BS EN 13501-1:2007+A1:2009. A1 materials are completely non-combustible and make no contribution to fire.
The fire resistance periods of Lignacite GP loadbearing and non-loadbearing walls are shown in Table 4, derived from the National Annex to BS EN 1996-1-2.
The fire resistance of loadbearing walls is influenced by the proportion of the load on a wall, which is annotated in the National Annex as a ≤1.0 or a ≤ 0.6. The fire values presented are based on the worst loading case (≤1.0) and can therefore be safely used for all loading conditions.
The thicknesses shown are for masonry alone, excluding finishes. For the fire resistance of walls with finishes, refer to the Lignacite Design Guide – Fire Resistance.
Table 4 – Fire Resistance
Solid blocks (Group 1 units) No finish | Non-loadbearing wall (criteria E1) | Loadbearing wall (criteria RE1) |
---|---|---|
100mm Lignacite GP - All strengths | 2 hours | 3 hours |
140mm Lignacite GP - All strengths | 4 hours | 3 hours |
Thermal Properties
The thermal resistance values (m² K/W) for Lignacite GP blocks are shown in Table 5. The values are calculated by dividing the block thickness by its thermal conductivity (W/mK).
Table 5 – Thermal Resistance Values
Thermal Resistance (m² K/W): 3% m/c | Thermal Resistance (m² K/W): 5% m/c | |
---|---|---|
100mm Lignacite GP - All strengths | 0.212 | 0.196 |
140mm Lignacite GP - All strengths | 0.298 | 0.274 |
(1) 3% moisture content (m/c) should be used for protected locations, such as the inner leaf, and 5% for exposed locations, such as the outer leaf when rendered.
Presented in the tables are the U-values for a range of wall constructions based on 100mm Lignacite GP blocks with full and partial cavity insulation. The outer leaf is facing brick, but a rendered block outer leaf will usually achieve at least the same U-value.
Full Cavity Fill and 100mm Lignacite GP Blocks
Cavity fill type | Internal finish - 12.5mm plasterboard on dabs U-values (W/m² K) | Internal finish - 13mm lightweight plaster U-values (W/m² K) |
---|---|---|
100mm DriTherm Cavity Slab 32 Ultimate | 0.26 | 0.27 |
125mm DriTherm Cavity Slab 32 Ultimate | 0.22 | 0.22 |
150mm DriTherm Cavity Slab 32 Ultimate | 0.19 | 0.19 |
100mm Isover CWS 32 | 0.26 | 0.27 |
125mm Isover CWS 32 | 0.22 | 0.22 |
150mm Isover CWS 32 | 0.19 | 0.19 |
90mm Kingspan Kooltherm K106 (plus a 10mm cavity) | 0.18 | 0.18 |
115mm Kingspan Kooltherm K106 (plus a 10mm cavity) | 0.15 | 0.15 |
140mm Kingspan Kooltherm K106 (plus a 10mm cavity) | 0.12 | 0.12 |
90mm Eurowall + (plus a 10mm cavity) | 0.19 | 0.20 |
115mm Eurowall + (plus a 10mm cavity) | 0.16 | 0.16 |
140mm Eurowall + (plus a 10mm cavity) | 0.14 | 0.14 |
100mm Xtratherm Cavity Therm | 0.19 | 0.19 |
125mm Xtratherm Cavity Therm | 0.15 | 0.16 |
150mm Xtratherm Cavity Therm | 0.13 | 0.13 |
Cavity fill type | Internal finish - 12.5mm plasterboard on dabs U-values (W/m² K) | Internal finish - 13mm lightweight plaster U-values (W/m² K) |
---|---|---|
60mm Celotex CW4000 | 0.25 | 0.25 |
75mm Celotex CW4000 | 0.21 | 0.22 |
100mm Celotex CW4000 | 0.17 | 0.17 |
60mm Kingspan Kooltherm K108 | 0.22 | 0.23 |
75mm Kingspan Kooltherm K108 | 0.19 | 0.19 |
100mm Kingspan Kooltherm K108 | 0.15 | 0.15 |
60mm Eurowall Cavity | 0.25 | 0.25 |
75mm Eurowall Cavity | 0.21 | 0.22 |
100mm Eurowall Cavity | 0.17 | 0.17 |
100mm Rockwool Partial Fill | 0.26 | 0.27 |
150mm Rockwool Partial Fill | 0.19 | 0.19 |
170mm Rockwool Partial Fill | 0.17 | 0.17 |
100mm Isover CWS 32 | 0.25 | 0.26 |
125mm Isover CWS 32 | 0.21 | 0.22 |
150mm Isover CWS 32 | 0.18 | 0.18 |
(1) The U-values shown are based on the use of various proprietary insulation products. Alternative products can be used, provided they can achieve an equivalent thermal resistance (m² K/W).
(2) Wall ties are assumed to be stainless steel with a cross-sectional area of no more than 12.5mm² for structural cavities up to 125mm wide.
(3) The suitability of full fill cavity insulation materials will depend on exposure conditions and should be confirmed by the designer. For partial cavity fill, a 50mm residual should be maintained (always check the manufacturer’s guidance).
Sustainability
Block Environmental Management and Responsible Sourcing
Our manufacturing plants operate to a BSI certified Environmental Management System (EMS), which complies with ISO14001.
Lignacite Ltd also meets the requirements of BES 6001 – Framework Standard for the Responsible Sourcing of Construction Products (Certificate No: BES 580823). This independently awarded Responsible Sourcing Certification confirms that our products have been made with constituent materials that have been responsibly sourced. This extends to organisational governance, supply chain management and environmental and social aspects, all of which must be addressed in order to ensure the responsible sourcing of construction products. Certification to BES 6001 will allow credits to be gained under environment assessment schemes such as BREEAM.
Block Energy Management
A BSI certified energy management system in accordance with ISO 50001 (Certificate No. ENMS 751020) is used to help manage energy use.
Compliance with ISO 50001 is a valuable tool in helping to manage energy use and includes the following outputs.
- A policy for more efficient use of energy
- Fix targets and objectives to meet the policy
- Use data to better understand and make decisions about energy use
- Measure the results
- Review how well the policy works, and
- Continually improve energy management
Block Environmental Performance Declaration (EPD)
Key environmental performance data (in accordance with EN 15804+A2 and ISO 14025/ ISO 1930) can be found in the EPD for Lignacite GP Blocks.
Environmental Data Summary
Declared unit | 1m² |
---|---|
Declared unit mass | 145 kg |
GWP-fossil, A1-A3 (kgCO2e) | 25.8 |
GWP-total, A1-A3 (kgCO2e) | 24.5 |
Secondary material, inputs (%) | 20.8 |
Secondary material, outputs (%) | 80 |
Total energy use, A1-A3 (kWh) | 47 |
Total water use, A1-A3 (m3e) | 1.36E0 |
Source – This data was taken from the EPD for the 7.3N Lignacite GP block. Click here for all EPDs.
The declared unit is based on 1m² of 100mm thickness blocks.
The Life Cycle Stage (A1-A3) refers to the extraction, processing, transportation and manufacture of materials and products up to the point where they leave the factory gate to be taken to site.
The notation ‘e’ is an abbreviation for tonnes of carbon dioxide equivalent.
Design
Block Structural Design
The design of walls using Lignacite GP concrete blocks should be in accordance with relevant design standards, including BS 8103: Part 2 and BS EN 1996-1-1 and the requirements of the Building Regulations.
Block Movement Control
Vertical movement joints should be considered in accordance with masonry design codes and the recommendations of Published Document PD 6697, at 6.0 - 7.0 metre spacings. In areas of increased stress, such as above and below openings in external walls, the blockwork may need to be reinforced to restrain movement.
Block Service Life
When properly constructed, the durability of walls built using Lignacite products will match that of traditional masonry and will fulfil their intended function for the life of the building in which they have been installed (typically 100 years).
The blocks themselves will require no maintenance. Maintenance for walls will normally include the replacement of sealant in movement joints and at junctions / openings. Repointing for walls that are exposed to the elements may be necessary towards the end of their service life.
Block Wall Ties
Under normal conditions, wall ties should be embedded 50mm into the mortar on each leaf, staggered in alternate courses and spaced in accordance with the following.
Table 6 – Wall Tie Spacings
Leaf Thickness (mm) | Cavity Width (mm) | Horizontal Spacing (mm) | Vertical Spacing (mm) | Ties per m² |
---|---|---|---|---|
Less than 90mm | 50 - 75 | 450 | 450 | 4.9 |
Over 90mm | 50 - 150 | 900 | 450 | 2.5 |
Block Mortar
Generally, the mortar type for work above ground level should be designation (iii) / Compressive Class M4. Designation (ii) / Compressive Class M6 is needed for work below ground in conditions where there is a risk of saturation with freezing.
Table 7 – Mortar Mixes
Mortar Designation (as per BS 5628-3) | Compressive Strength Class (as per BS EN 1996) | Recommended mix proportions of materials by volume |
---|---|---|
(iii) | M4 | 1:1:5 to 6 - Cement:Lime:Sand. 1:5 to 6 - Cement:Sand with or without air entrainment. 1:4 to 5 - Masonry Cement:Sand (with non-lime filler). 1:3½:4 - Masonry Cement:Sand (with lime filler). |
(ii) | M6 | 1:½:4-4½ - Cement:Lime: Sand. 1:3 to 4 - Cement:Sand with or without air entrainment. 1:2½:3½ - Masonry Cement:Sand (with non-lime filler). 1:3 - Masonry Cement:Sand (with lime filler). |
Site Practice
Block Surface Finish Recommendations
Drylining
Standard plasterboard can be fixed with adhesive dabs or onto timber battens or metal studs.
Plaster
Dense plasters can be applied using either 1:1:6 cement:lime:sand or 1:4 ½ masonry cement:sand or 1:5 ½ cement:sand and plasticiser. It is advisable to use a bonding treatment prior to applying cement render plasters.
Lightweight plasters should be used in accordance with the manufacturer’s recommendations. Suitable plasters include British Gypsum’s Thistle Hardwall.
Finishing coats include British Gypsum’s Thistle Multi-Finish.
Rendering
Lignacite GP has moderate absorption. The textured surface aids the adhesion of plasters and renders.
Before rendering, all dirt and debris must be removed from the surface. Traditional renders should be applied in 2 coats with the first coat applied to a greater thickness than the top coat (the first coat should be 8-12mm thick and the top coat 6-8mm). Render designation iii/M4 should be used, as shown in Table 8.
It is important that blocks are protected from the weather prior to and during rendering.
Table 8 – Render Mixes
Cement: Lime: Sand (with or without air entrainment) | Cement: Sand (with or without air entrainment) | Masonry Cement: Sand (with non-lime filler) | Masonry Cement: Sand (with lime filler) |
---|---|---|---|
1 : 1 : 5 or 6 | 1 : 5 or 6 | 1 : 4 or 5 | 1 : 3½ to 4 |
Builders considering the use of proprietary render systems must exercise caution and accurately adhere to the render manufacturer’s design and specification instructions. Detailed guidance is also published in the NHBC Standards, Chapter 6.11- Render. Strictly adhere to the specific application instructions, paying particular attention to prevailing weather conditions and the minimum recommended thickness of single coat renders.
Block Safe Handling
For detailed advice, refer to Lignacite’s Sitework Guide and the Material Safety Datasheet.
- Block packs may be stacked on firm and level surfaces to a maximum height of 2 packs. Consideration of handling equipment’s suitability for site terrain and safety limits should also be given. Hand-operated pallet trucks may not be suitable unless pallets specific for this purpose are used and loads do not exceed the limits of the pallet truck or its operator(s). Care should be taken when opening packs that are wrapped or banded to ensure that items do not fall or otherwise endanger persons handling the blocks or those nearby.
- Handling of blocks should be undertaken in accordance with HSE Construction Sheet No. CIS77 ‘Preventing injury from handling heavy blocks’ (Construction Industry Advisory Committee) and in accordance with the Manual Handling Regulations 1992 (as amended). This concludes that there is a high risk of injury to individuals who repetitively manually handle blocks in excess of 20 kg. Where practical, mechanical handling equipment should be used to transport block packs to the area of work.
- Blocks should not be installed if the temperature is at or below 3°C and falling.
- Blocks should always be laid on a full bed of mortar and vertical joints solidly filled.
Product Resources
Take a look at our handy downloadable guides, designed to help you get the best from our concrete blocks.
1 of 4