Articles
The role of manufacturing in life cycle assessment
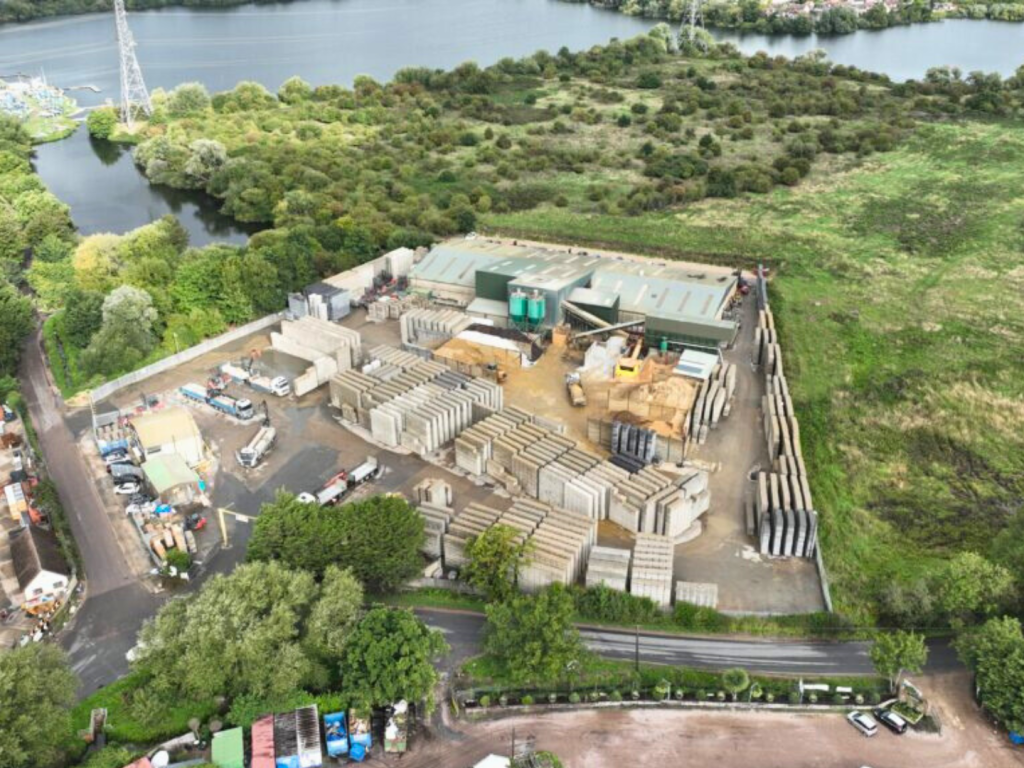
Posted by Lignacite
In the construction industry, sustainability is no longer a bonus feature – it’s an expectation. According to research, the built environment is responsible for around 25% of the UK's greenhouse gas (GHG) emissions, which rises to 42% if surface transport is included. As the construction sector works to meet net-zero targets and reduce its environmental footprint, Life Cycle Assessment (LCA) has become a key tool. It helps quantify the environmental impact and carbon footprint of a building from cradle to grave, including manufacturing.
Understanding life cycle assessment in construction
Life Cycle Assessment (LCA) considers the full environmental impact of a building over time – from site selection and material sourcing, through construction and use, to demolition and end-of-life outcomes. It accounts for every stage of the building’s journey, including whether materials can be reused or recycled once the building reaches the end of its useful life.
The process is guided by international standards, notably ISO 14040 and ISO 14044, which provide a framework for conducting LCA studies in a consistent and systematic way.
Each phase of the life cycle is categorised using a lettering system from A to D, with an additional Stage E sometimes used to capture benefits, such as reuse or energy recovery. The early product stages focus on the materials used to construct a building and are grouped under Stage A, which is further divided into A1 to A4.
These early phases are typically considered during the design phase of a project. Architects and specifiers – often with input from sustainability consultants – assess factors such as material selection and site suitability right from the outset. This is particularly important for projects pursuing BREEAM certification or similar sustainability credentials, where early decisions can influence the building’s environmental rating.
Manufacturing's critical role in LCA
Because LCA takes a holistic view of a building’s environmental impact, it places significant emphasis on the manufacture of construction materials. This includes everything from how and where raw materials are sourced, to the energy and resources used during production, and how the final products are transported.
These impacts are typically captured in a third-party verified Environmental Product Declaration (EPD). This is a standardised document that presents the data in a clear, accessible format. A range of digital LCA tools and platforms now make it easier for architects and specifiers to analyse EPDs and compare the environmental performance of different building materials.
A1: Raw material extraction
The first stage of the LCA manufacturing phase focuses on the origins of the materials used in a product. It considers whether materials are extracted directly from the natural environment or whether secondary or recycled sources are used. This stage also evaluates the carbon emissions, water consumption and other environmental impacts associated with extraction.
At Lignacite, we prioritise the use of secondary and recycled materials, including graded wood particles, wherever possible. All of our raw materials are sourced in accordance with BES 6001, which sets out criteria for the responsible sourcing of construction products.
A2: Transportation of raw materials
Once materials are extracted or recycled, they typically need to be transported to a separate location for processing or manufacturing. This movement consumes energy and generates emissions. For this reason, transportation plays a key role in calculating a product’s embodied carbon and must be included in the LCA.
At Lignacite, we source materials locally wherever possible to reduce transport distances and associated emissions. In addition, all on-site vehicles are powered by hydrotreated vegetable oil (HVO), a renewable fuel that can produce up to 90% lower emissions compared to conventional diesel.
A3: Manufacturing
The manufacturing stage focuses on how raw materials are transformed into finished products. This part of the LCA assesses the energy used during production – such as electricity, gas, and heat – as well as waste generation and any process emissions. These impacts vary depending on the equipment used, operational efficiency, whether renewable energy sources were used and the steps taken to reduce environmental harm.
At Lignacite, we’ve made significant investments to make our manufacturing processes more sustainable. When our Brandon factory opened in 2023, it was specifically designed to minimise fossil fuel use and reduce carbon emissions. The facility features solar panels, heavily insulated curing chambers, and an on-site water source to limit reliance on external supply. Power factor correction helps optimise electricity use, and smaller mixer sizes reduce the likelihood of excess material and waste. These improvements reflect our ongoing commitment to lowering our environmental impact at every stage of production. You can find out more about the Lignacite Brandon factory on our website.
A4: Transportation of manufactured products
The final part of the manufacturing stage involves transporting finished products to the construction site. As with Stage A2, this step uses energy and generates emissions – both of which contribute to a product’s overall embodied carbon.
At Lignacite, we offer HVO-powered delivery vehicles for routes within the London area, helping to cut emissions by up to 90% compared to standard diesel. We also optimise delivery routes to maximise efficiency, reduce mileage and minimise unnecessary journeys – all contributing to lower environmental impact across our supply chain.
The impact of manufacturing on other LCA stages
The environmental impact of construction materials doesn’t stop once they’re delivered to site. The choices made during manufacturing can influence every subsequent stage of a building’s entire lifecycle – from how it performs in use, to how it is repaired, replaced, or eventually deconstructed.
For example, around 48% of emissions from the UK’s built environment come from energy use in existing homes. Materials that are airtight or offer good thermal insulation can help reduce this figure by improving a building’s energy efficiency. This is particularly relevant to Stage B6 of the LCA, which assesses operational energy consumption during the use phase.
Materials must also stand the test of time. If they deteriorate quickly and need to be repaired or replaced, this introduces additional impacts under Stages B3 and B4 – covering repair and replacement. These activities involve further material use, energy input and waste generation, all of which add to the building’s lifetime footprint. An important advantage in specifying concrete blockwork is that it will require little to no maintenance throughout its service life.
At the end of the building’s life, materials are assessed again under Stage C. This includes demolition, waste processing and disposal. Products that can be recycled or repurposed offer clear advantages at this stage.
Lignacite blocks, for example, can be crushed and reused as hardcore for road construction or even reincorporated into new blocks – contributing to a more circular approach to construction.
LCA for manufacturing and green building certifications
Life Cycle Assessment plays a vital role in achieving sustainability certifications such as BREEAM (Building Research Establishment Environmental Assessment Method) and LEED (Leadership in Energy and Environmental Design). While LEED is more commonly used in the US, BREEAM is widely adopted in the UK and Europe.
BREEAM assesses individual elements of a whole building – including materials – to award up to six LCA credits for responsible product sourcing and environmental performance. An additional three innovation credits may be available for particularly forward-thinking approaches. These certifications provide independent verification of a building’s sustainability credentials, making them increasingly important for both public and private sector developments.
Regulatory pressure is also mounting. Since 2020, Whole Life Carbon Assessments (WLCA) have been mandatory for public construction works in the UK, supporting the Government’s target of reaching net zero by 2050. In London, the Greater London Authority’s London Plan Policy SI 2 goes further, requiring developers to calculate and reduce whole life-cycle carbon emissions before construction begins.
Looking ahead, a proposed addition to the UK Building Regulations – known as Part Z – may soon require whole-life carbon reporting for all new buildings over 1,000m² or developments with more than 10 dwellings. Although not yet law, its introduction would mark a significant shift towards embedding LCA into mainstream building practice.
Build better from the start
Manufacturing and construction are deeply interconnected. Without the innovation and progress driven by the manufacturing sector, the construction industry would have fewer sustainable options to choose from. As the demand for low-carbon building solutions grows, manufacturers are increasingly focused on sourcing more sustainable materials and reducing the environmental impact of production.
At Lignacite, this commitment underpins everything we do. We continue to refine our manufacturing processes and delivery logistics to support a more sustainable construction industry – helping clients build better from the very beginning.
Alongside this, our new Lignacite ECO range reflects this forward-thinking approach. These blocks are made using up to 70% recycled materials and offer up to 70% lower embodied carbon than other types of masonry, helping you construct more sustainable buildings.