Articles
Product News
Sustainability newsletter!
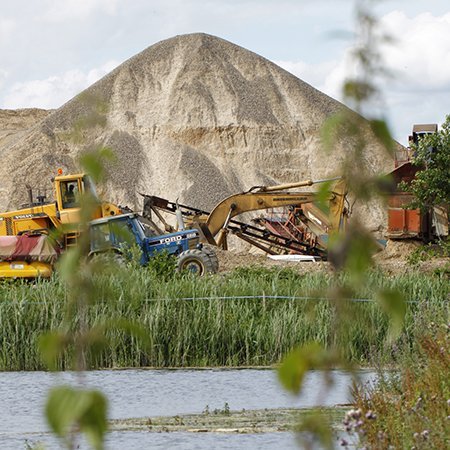
Posted by Nick Franks
Sustainability – A manufacturers responsibility
The construction industry in the UK accounts for approximately 60% of materials used and one third of all waste generated. Concrete blocks make a significant contribution to the built environment and as a result sustainability is fully integrated into the operations of Lignacite. The commitment goes beyond legislation and voluntary actions help to make our products and operations more sustainable. Designers or contractors can specify and procure concrete blocks produced by Lignacite with confidence.
Due to its inherent sustainable properties, the use of concrete blocks will result in buildings that are resilient, safe, strong, and adaptable and have a long lifespan compared to other forms of construction.
Environmental Commitment
Lignacite offers a full range of manufactured concrete blocks for industrial and commercial customers throughout the British Isles.
It ensures that manufacturing potential is maximised through the reuse of otherwise waste materials thus reducing the overall impact on landfill and subsequently minimising the impact upon the environment.
Working in conjunction with suppliers and customers, Lignacite continually looks for ways to improve their environmental performance by controlling and managing the operational activities and products. These activities include amongst other things, responsible sourcing of materials though the principals of BES 6001, the completion of environmental targets and objectives as well as maintaining certification to the environmental standard ISO14001. Raw materials are used efficiently through quality control practices that is overseen by a BSI certified ISO 9001 Quality Management System.
Improving and Monitoring Sustainability Performance
Working closely with organisations such as the British Precast Concrete Federation and the Concrete Block Association, Lignacite continues to develop, monitor and improve its sustainability performance.
Lignacite is a signatory to the British Precast Concrete Federation ‘Sustainability Charter’.
The aim of the Charter is to encourage member companies of British Precast to go beyond legislation and take voluntary actions to make their products and operations more sustainable. In order to meet this aim, a set of sustainability principles has been developed based on the key sustainability issues facing the precast industry; these issues are shown in the diagram, and were identified by British Precast following consultation with the industry and examination of the priorities and concerns of its primary stakeholders.
Courtesty of British PreCast Society
An important part of the commitment is to allow British Precast to audit member companies’ sites annually to ensure that all the 16 principles are being adhered to by member companies. A recent milestone was the publishing of an Environment Product Declaration (EPD) for aggregate blocks. Data contributed by Lignacite led towards the (EPD) and the data provided is independently verified and the registered document communicates transparent and comparable information about the life-cycle environmental impact of products. At end of product life, all of Lignacite concrete blocks are fully recyclable and will always almost certainly be recycled into aggregates for use as hard-core or piling mat at the demolition site or other construction sites.
Use of Recycled Raw Materials
Lignacite has a long history to support its commitment to the use of recycled and secondary aggregates in the production of its range of concrete products, with the original Lignacite block, first produced in 1947, which used a proportion of graded wood particles as part of its constituents. This is still the case today.
There are social, economic and environmental benefits that can be attributed to the use of recycled and secondary aggregates (RSA), providing of course that the quality of the recycled and secondary aggregates is fit for purpose and meets the published specifications. These benefits are not only conferred on the manufacturer but also society at large.
Examples of the use of RSA’s by Lignacite include furnace bottom ash, crushed glass and graded wood particles, and they are continually investing in new technologies to allow more use of RSAs in their production.
Thermal Mass & Insulation
There is an urgency to design and build structures that can cope with predictions for future climate change. It is therefore entirely appropriate to consider passive technologies that can be used instead of energy intensive air conditioning. Increasingly, design teams are incorporating the use of thermal mass into their structures. All Lignacite’s products have the potential to contribute to a design solution that can prevent overheating and provide a more comfortable internal environment.
For many building types, including commercial buildings and dwellings, a more sustainable solution to combat the risk of overheating is to utilise high thermal mass elements together with night cooling. This approach, also known as fabric energy storage (FES), typically focuses on the building’s thermal mass optimised by using fair faced blockwork as well as exposed concrete floor slabs. The walls and floors absorb heat, helping to reduce overheating and ensuring a more stable internal temperature. Night-time cooling purges the stored heat from the walls and the slabs, preparing it for the next cycle.
The proposals to amend Part L Thermal Standards of the Building Regulations offers a real challenge to the construction industry. The Government has issued a consultation ‘The Future Homes Standard’ which sets out what a home built to the Future Homes Standard will be like. It is anticipated that by 2015 an average home built to it will have 75-80% less carbon emissions than one built to current energy efficiency requirements (Approved Document L 2013). It is expected this will be achieved through very high fabric standards and a low carbon heating system. This means a new home built to the Future Homes Standard might have a heat pump, triple glazing and standards for walls, floors and roofs that significantly limit any heat loss. The first step is to introduce improved measures before the end of 2020. This may include;
Option 1: 20% reduction in carbon emissions compared to the current standard for an average home. We anticipate this could be delivered by very high fabric standards (typically with triple glazing and minimal heat loss from walls, ceilings and roofs).
Option 2: 31% reduction in carbon emissions compared to the current standard. We anticipate this could be delivered based on the installation of carbon-saving technology such as photovoltaic (solar) panels and better fabric standards, though not as high as in option 1 (typically double not triple glazing).
In terms of the building fabric it is clear that some changes to current practice will be required, but masonry construction can be adapted relatively easily, with little or no change to current building practice. A real dilemma is the balance between even higher fabric standards and the ability of homes to have adequate ventilation and built-in measures, including but not limited to, thermal mass, to combat the consequences of summertime overheating. The consultation finishes in March 2020 after which Lignacite will be publishing wall solutions capable of meeting the next generation of thermal standards.
Responsible Sourcing
Lignacite is certified to the Building Research Establishment (BRE) Framework Standard for the Responsible Sourcing of Construction Products – BES 6001.
This certification means that concrete masonry products supplied by Lignacite are responsibly sourced, to an independently verified standard that addresses the social, economic and environmental impacts across the entire supply chain.
Under the BES 6001 Framework Standard, Lignacite’s products have been assessed by looking at existing quality, environmental, health and safety management systems together with other important criteria including: greenhouse gas emissions, resource use, waste and water and life cycle assessment.
The certification also allows for traceability of the product to ensure all areas within the supply chain are operating to high standards.
This provides customers with confidence that the production and supply chains are operating ethically and responsibly, it also allows them to score more credits under the materials section of the BREEAM and other environmental assessment schemes such as LEED, or Leadership in Energy and Environmental Design.
The BES 6001 certification is part of Lignacite’s commitment to sustainable development and complements a range of other ongoing initiatives to reduce waste, water, energy use and CO2 emissions.
Using Lignacite Blocks
AshGP, Lignacite and Lignacrete blocks can be used to construct cavity separating walls meeting the requirements of Building Regulations as well as the requirements of a number of Robust Detail specifications. Solid separating walls can be built using Lignacrete blocks. A number of specifications are also available that are capable of achieving higher standards of sound insulation than those given in Approved Document E to the Building Regulations. These are generally in accordance with certain Robust Detail specifications and can be used to gain credits for improved sound insulation.
For further information on the products and services offered by Lignacite, please visit our contact us page or call 01842 810678.