Articles
Insulating concrete block walls: a guide
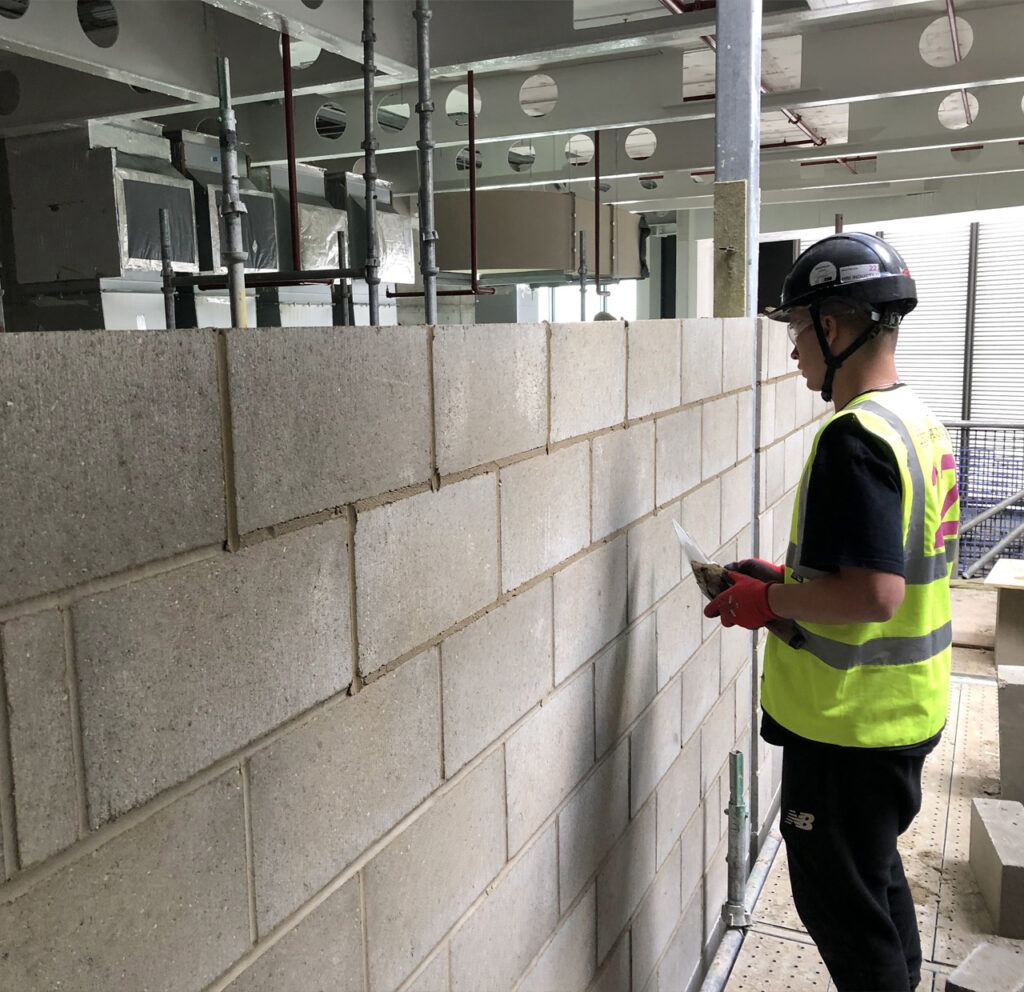
Posted by Lignacite
Insulating concrete block walls is an important step when creating energy-efficient buildings, whether you’re constructing a house or a commercial property. With rising energy costs and stricter Building Regulations, ensuring that walls are properly insulated not only saves money but also improves comfort and sustainability.
In this guide, we’ll cover everything you need to know about insulating concrete block walls, including why it’s necessary, the materials available and tips for installation.
Do concrete block walls need to be insulated?
Yes, concrete block walls should be insulated. Both residential and commercial buildings must meet insulation standards set out in the Building Regulations. Under Part L, external walls in residential new builds must achieve maximum U-values of 0.18 W/m²K, a measure of heat loss.
The same standard of insulation will also apply to semi-exposed walls, such as between a dwelling and an integral garage. Insulating these walls reduces heat loss, improves energy efficiency and helps lower running costs for the building.
Concrete blocks offer some natural insulative properties, but will not meet modern energy standards on their own. The thermal insulation of any material is measured by its thermal resistance (m2K/W) or R-value, which indicates resistance to heat flow for a given thickness. The higher the R-value, the better the insulation. A standard 100mm medium-dense block has an R-value of around 0.20, offering some resistance to heat transfer.
For comparison, high-performance insulation materials like mineral wool or polyurethane boards achieve R-values between 2.5-5.0 for the same thickness. These figures highlight the need to combine concrete blocks with dedicated insulation to enhance thermal performance. This combination also improves the airtightness of the building envelope, further supporting energy efficiency and comfort.
Types of insulation used for concrete block walls
In UK construction, two primary types of insulation are used for concrete block walls: mineral wool and rigid insulation boards. Both of these products have properties that minimise heat loss by slowing down heat passing through the material.
Mineral wool
Mineral wool is made by melting silica or stone until it becomes molten, then spinning it into a wool-like material. Flexible and non-combustible, it is highly effective in high-rise buildings and attic spaces, where fire resistance is critical. Mineral wool provides excellent thermal performance while maintaining structural integrity when fitted between walls. Mineral wool batts are installed into the cavity as the walls are built. It is also possible to inject mineral fibre into the cavity after the walls have been built, however this is not usually as thermally efficient as mineral wool batts.
Insulation boards
Insulation boards are typically made of rigid polyurethane or polyisocyanurate with reflective surfaces, and are collectively known as PIR boards. During manufacture, the PIR foam goes through a chemical reaction, resulting in a closed-cell structure that traps gas. This gas conducts less heat than still air, resulting in a thermally efficient insulation product.
PIR boards are suitable for use in full or partial-fill cavity wall applications, allowing for optimal thermal performance to be achieved.
Because of their superior thermal conductivity – typically around 0.022 W/mK – PIR boards are the best option to minimise the width of the cavity. This is usually 100mm for full fill and 150mm for partial cavity fill applications. Where the cavity is to be fully filled with insulation, the type of insulation, its thickness and the wall construction should be suitable for the exposure of the home. Guidance can be based on local practice, but new homes will have to comply with the technical requirements issued by the NHBC and other insurance providers.
However, to meet regulatory standards to limit the spread of fire, PIR boards are not advocated in the external walls of buildings over 11 metres in height.
Other insulation options
In addition to mineral wool and rigid insulation, other options are available, although they are more commonly used to insulate existing masonry walls:
Spray foam insulation: Made from polyurethane, spray foam is sometimes used but is often avoided due to safety concerns and higher costs. It is unsuitable for listed properties.
Injection foam insulation: This involves drilling small holes into existing walls and injecting polyurethane foam into the cavity. Professional installation is required.
Polystyrene bead cavity wall insulation: Polystyrene beads are poured into wall cavities to create an effective insulation layer.
These options all have pros and cons, so it’s important to choose the right method for your building's needs.
Insulating concrete block walls
Typically, insulation is used in cavities between walls. In the case of boards, these will be clipped between the leaves to hold them in place. Mineral wool tends to hold its shape and structure when pushed between the leaves.
To avoid thermal bridging during installation, ensure the insulation forms a continuous layer without gaps or interruptions, particularly at junctions between walls, floors and roofs, as well as around windows and doors.
Use insulated wall ties or clips to secure materials in cavity walls, and seal any joints or gaps with appropriate tapes or sealants. Structural elements like steel beams or lintels should be wrapped in insulation or replaced with thermally broken components to minimise heat transfer.
Properly installed insulation not only improves energy efficiency but also reduces the risk of condensation and damp.
Want to know more about using our blocks in your next project?
Give our Quoting Team a call to discuss your needs and arrange a quotation.