Articles
Building a Sustainable Future with Lignacite Concrete Blocks
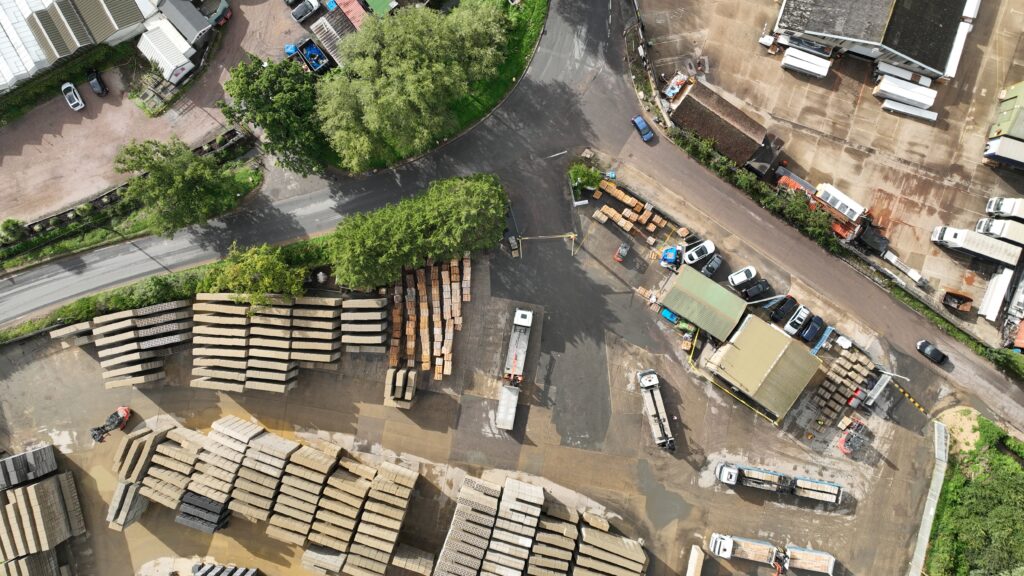
Posted by Nick Franks
How can concrete blocks fit into sustainable building design? In this article, we examine whether concrete blocks can be sustainable and what we’re doing to make our building materials greener.
Since we began manufacturing our blocks in 1947, we have had an ethos of recycling and reusing.
The very first concrete building block we manufactured contained recycled wood particles, a unique aggregate that continues to be a key ingredient in our flagship blocks today. This established our greener manufacturing methods, and we have gone on to use many other recycled materials within our blocks.
However, we know that we need to do more. For this reason, we have made a pledge to reach net zero by 2030, 20 years before the government’s deadline.
So, can concrete blocks remain a part of the story when it comes to sustainable design? Let’s take a closer look at what the concrete industry is doing to encourage more eco-friendly manufacturing.
Are concrete blocks sustainable?
The manufacturing process needed to create concrete blocks certainly generates a carbon footprint. However, ongoing research and development means that manufacturers are exploring new methods and materials to make this versatile building material more sustainable.
Recycled aggregates are already being used in their manufacture to reduce the reliance on virgin constituents. For instance, pulverised fuel ash and recycled wood particles are already being used in our blocks. Concrete bricks and blocks manufacturers are also beginning to experiment with using solar power to fuel their plants. Our own facility in Brandon has 12% of its electricity supplied in this way.
Concrete blocks may also be seen as a sustainable material because they can be recycled. Our concrete blocks, for instance, can be ground up and reused at the end of their lifespan.
There is also a theory that concrete blocks can absorb carbon dioxide over the course of their use. This process is called carbonation, and it could mean that concrete products help to ‘lock in’ carbon emissions. However, research on this is still in its infancy.
You can find out more about the research into sustainable concrete blocks in our detailed article.
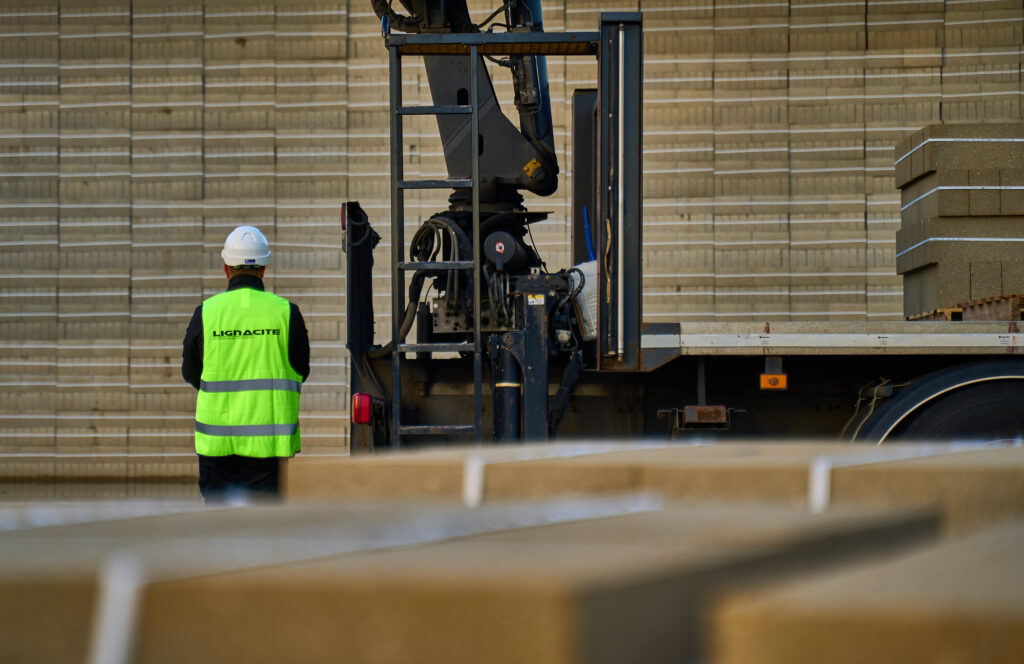
What is Lignacite doing to make their concrete blocks more sustainable?
Thanks to our ambitious 2030 net zero goal, we have been working towards reducing our emissions to make our production methods more sustainable.
Here are just some of our actions so far.
Reduction in energy use
We have increased our energy efficiency on site, which has led to a drop in the amount of electricity needed to produce our blocks. In 2020, 1.04kWh was used for each square metre of product. In 2022, this was cut to 0.77kWh.
New monitoring systems and ISO 50001 processes have also reduced our natural gas use to just 0.05kWh per square metre of product. Meanwhile, use of liquid petroleum gas has been cut to zero.
On-site plant vehicles switched from diesel to HVO
All 25 of our on-site plant vehicles have now been switched to hydrotreated vegetable oil (HVO). This fuel has 90% of the carbon emissions of white diesel, saving us 440 tonnes of carbon every year.
Increasing recycling
By focusing on our use of materials, we have identified more situations for recycling. This led to 17,638 tonnes of waste being recycled in 2022, up from the 7,718 tonnes that were recycled two years previously.
Improving efficiencies
Boosting efficiency is a great way to reduce energy consumption. Prioritising efficiency has been particularly useful when it comes to our transport.
By carefully planning our routes, we have increased the volume of blocks we can deliver per kilometre. In 2022, we decreased our total distance travelled by 12.1% from 2018. Over the same period, we increased the total volume of blocks delivered by 58.9%.
Find out more about our concrete block sustainability
If you’d like to find out more about our sustainable goals and how we are working towards them, take a look at our in-depth case study.