A Factory for the Future
Our new state-of-the-art facility brings benefits to customers and the environment.
1 of 3
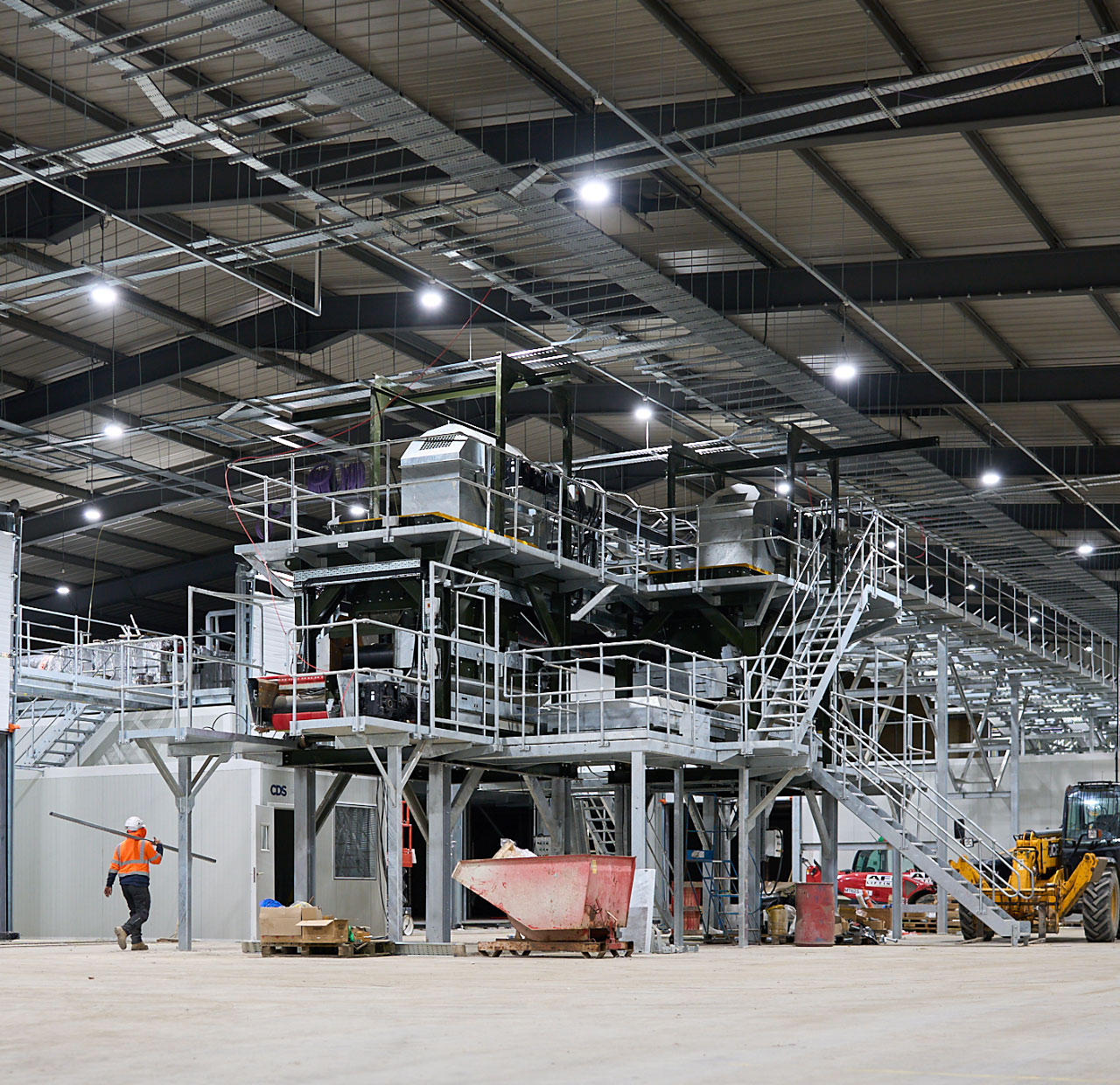
We haven’t just paid attention to the production line
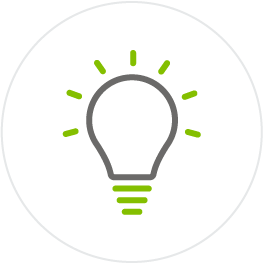
Light
Light to the facility is supplied by a low-energy system.
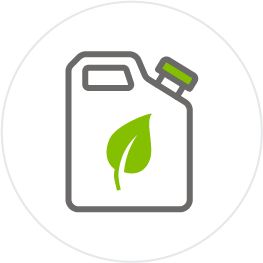
Fuel
Forklifts powered by HVO fuel do the heavy lifting.
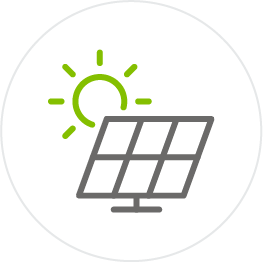
Energy
Solar panels provide the factory with an ongoing supply of renewable energy.
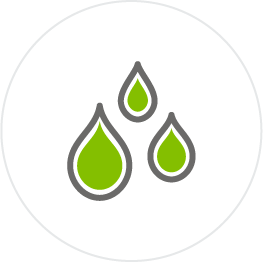
Water
Water to the facility is also sourced on-site, thanks to our very own borehole.
The Result?
Even better service and products for our customers and reduced energy and waste for us.
Want to know more? You can see our factory build unfold by watching this video.