Articles
How eco friendly is concrete? Decarbonising the industry
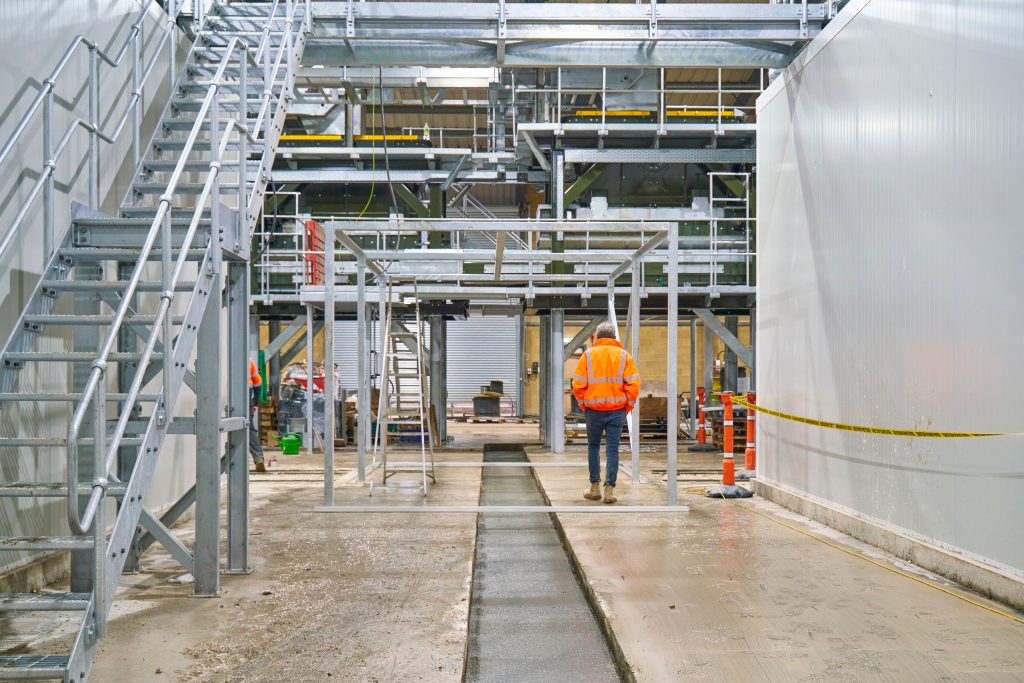
Posted by Nick Franks
In this detailed article, we take a deep dive into the concrete industry and explore its plans to decarbonise. Read on to find out more about how eco-friendly concrete is.
As a building material, concrete is favoured across the globe. Robust, long-lasting and non-combustible, it contributes towards the construction of homes, schools, commercial buildings and leisure facilities.
But this comes at a cost. According to the Mineral Products Association (MPA), concrete and cement (a key ingredient in concrete) currently account for around 1.5% of the UK’s carbon dioxide emissions. In 2018, our CO2 emissions from these materials stood at 7.3 million tonnes.
This is because raw materials for traditional concrete must be extracted, crushed and transported. The process of making cement, which is later mixed with other aggregates to create concrete, then requires a great amount of heat, much of which is still provided by fossil fuels. For instance, Portland cement is heated to 1,488 degrees Celsius. The finished product is then transported to the construction site, which adds a further burden of emissions to its total.
However, this does not mean that progress is not possible. Indeed, great strides have already been made in the concrete and cement industry. According to the MPA, since 1990 the UK cement and concrete industry has reduced its carbon emissions by more than half.
How eco-friendly is concrete?
While the manufacture and transport of concrete are certainly notable drawbacks in terms of the eco-friendliness of concrete, there are other advantages.
For instance, concrete construction can benefit from its thermal mass. Concrete blocks can absorb excess heat during the day before releasing it at night, curbing the need for energy-intensive artificial means of heating and cooling.
Concrete also theoretically has the ability to absorb carbon dioxide during its lifetime. This process is called carbonation. This is where rainwater and air interact with the surface of the concrete, absorbing carbon dioxide from the air. The result is a chemical reaction that transforms calcium hydroxide within the concrete into calcium carbonate. This traps carbon dioxide within the structure of the concrete, in addition to strengthening it.
Concrete is recyclable too. The Building Research Establishment’s (BRE) Green Guide estimates that 50% of concrete is currently crushed and recycled and 40% is downcycled (for use in roads, for example).
With regards to the energy used to make concrete, manufacturers are also exploring renewable energy solutions, such as solar polar. There is also some interesting research being carried out into low-carbon alternatives to common aggregates and cement.
Low-carbon cement and aggregates
Recycled, and therefore low carbon, aggregates are already on the market and are being used in sustainable concrete manufacture today. For instance, in our Lignacite range, we use recycled wood particles.
Straw ash, ground granulated blast furnace slag and limestone are also great sustainable options in concrete production. These materials reduce embodied carbon because they can be used with smaller amounts of Portland cement, one of the most common types of cement.
The British Standards Institute has now, in fact, promoted the increased inclusion of these materials in concrete production, limestone in particular. The new standards BS8500-1 2023 and BS8500-2 2023 will help UK adopters of BS EN206 (European concrete specification standard), and allow greater use of limestone powder within the concrete mix.
If adopted across all UK construction sites, it’s estimated that this could reduce carbon dioxide emissions by one million tonnes every year.
Other innovations are also well underway. For instance, the MPA is now working with Hanson Cement, Forterra Building Products and the BRE to develop and test low-carbon cement. Some of the products currently being tested have 55% lower embodied carbon dioxide than traditional concrete such as Cem 1.
Other promising sustainable concrete materials include:
- Hemp: Mixed with water and lime, hemp can be used to create green concrete that has excellent thermal performance, strong carbon sequestration properties, and is fully recyclable at the end of its life. The fact that it is easy and fast to grow also means that it takes out more carbon from the atmosphere than that produced using its application.
- Plastic waste: Readily available, research is looking into using plastic in concrete to reduce waste in landfills.
- Micro-silica: A by-product of industrial manufacture, when added to concrete micro-silica can improve strength and durability.
- Coffee: Using processed coffee grounds could reduce the amount of sand needed in concrete as well as cut food waste. Another plus point is that early research has shown that the inclusion of coffee grounds can increase concrete’s strength by nearly 30%.
The future of concrete blocks
As we look toward the future, it is certain that concrete and cement manufacturers will need to find more sustainable solutions for their products. “The world is changing. Many people are far more conscious of the harm we do to the environment than they were 10 years ago,” explains Marvyn Candler, Lignacite’s SHEQ Manager. “As time goes on, this awareness will only increase.
“The pendulum has been swinging faster and faster towards the need for greener buildings for some time and it isn’t going to swing back. The time will come when cement-based blocks just won’t be accepted. This won’t happen just yet, but I estimate that this will be the case within 20 years.
“The focus needs to be on creating a truly green, sustainable block. This means increasing our use of recycled materials and reducing our use of primary aggregates down to an absolute minimum, ultimately aiming for zero percent.”
Here at Lignacite, we are committed to helping this movement by reaching net zero by 2030. This is a full 20 years before the government’s mandate.
Currently, we are working on an eco block, which contains much higher recycled content than the products in our standard ranges. We are also exploring replacing cement with an environmentally friendly alternative. In addition, we have been looking at using rubble from demolished buildings and adding them to the concrete mix, although there is the risk of contamination from asbestos and metal, so this may not be viable.
However, as Marvyn points out, replacing the materials in concrete is not the only variable that must be considered: “For a block to be truly green and eco-friendly, we need to change the way we operate.
“We need to achieve carbon neutrality and increase our use of renewable energy sources. The way people work also needs to change, such as increasing the use of video conferencing services for fewer road trips, switching to the digital storage of files and reducing our reliance on printed matter.
“We need to reduce waste in all that we do, wherever possible. If we make these changes then we can indeed produce a truly green block.”
To assist with this, we have already switched all of our on-site plant vehicles to HVO, a green alternative to white diesel. LED lighting, solar power, better route planning and a new highly efficient factory are also helping us towards this goal.
This is already producing results with carbon emissions across the business dropping by 26.6% in the year 2024. Diesel use at our Brandon and Nazeing bases has also dropped by 45% and 23.6% respectively over the same period.
Find out more about our sustainability journey so far in our detailed case study.
Learn more about our concrete blocks
If you’d like to find out more about Lignacite's sustainability credentials and carbon footprint, you can browse the sustainability section of our website or head to our sustainability reports and certificates.
Alternatively, get in touch with our friendly team by calling 01842 778485.