Articles
Are concrete blocks sustainable?
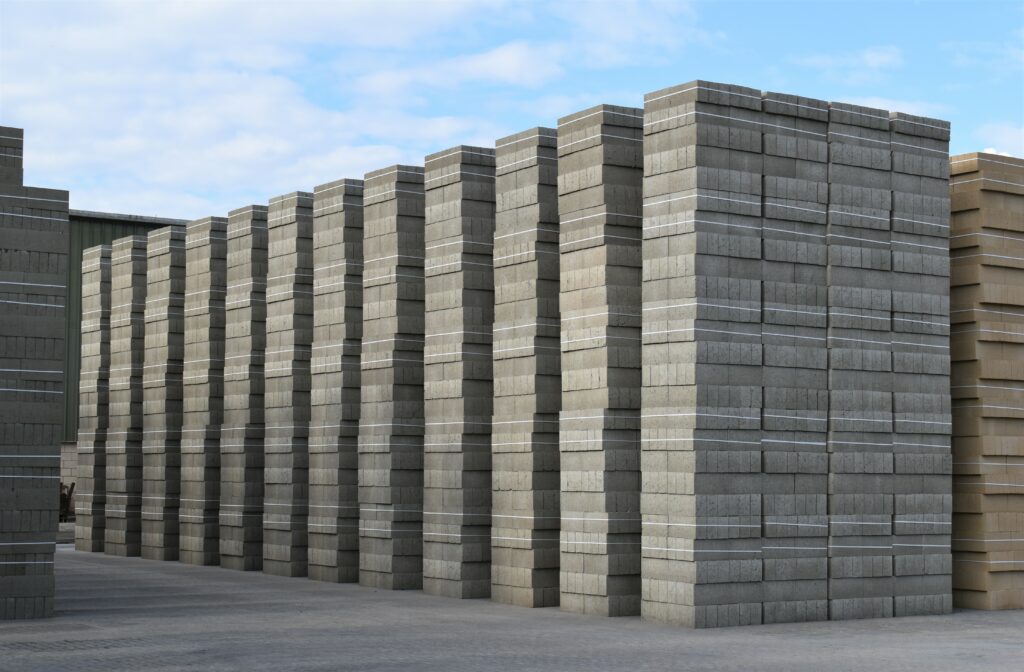
Posted by Nick Franks
Concrete blocks are a popular and durable building material. But how sustainable are they? We look into the carbon footprint of cement, the thermal efficiency of blocks and sustainable concrete mixes.
Concrete blocks are popular for a reason. They are strong, long-lasting and readily available. But in a world looking for greater sustainability, where do they fit in?
To find out, we’ve taken a closer look at this versatile building material and how we, and the industry as a whole, are moving towards greener solutions.
Are concrete blocks sustainable?
Concrete production certainly creates a carbon footprint and has an impact on our environment. However, concrete blocks do theoretically have the ability to absorb carbon dioxide throughout their lifetime.
This is due to a process called carbonation.
On paper, this means that as rainwater and air interact with the concrete's surface over time, carbon dioxide from the air is absorbed. This leads to a chemical reaction that transforms calcium hydroxide within the concrete into calcium carbonate. This transformation may strengthen the concrete and also could trap carbon dioxide within its structure.
This hypothetically means that concrete products could absorb CO2 from the atmosphere during their lifetime of 100-150 years. It has even been suggested that the carbonation process could absorb around a third of the CO2 emissions produced during the making of cement used for concrete.
Our flagship Lignacite blocks also contain recycled wood particles. Not only is this a sustainable material, but the wood could also help to ‘lock in’ even more carbon. This may reduce the carbon footprint of our blocks even further.
Having said this, research into the carbonation of concrete blocks has so far not produced any definitive calculations. We therefore need to watch this space.
Are concrete blocks environmentally friendly?
Like many other construction materials, concrete blocks require raw materials and energy in their production. However, huge strides have been made to make them more environmentally friendly.
Aggregates are a major ingredient in the manufacture of concrete blocks, but the good news is that lower-carbon alternatives can be used. For instance, air-cooled blast-furnace slag and crushed concrete aggregates are useful, recycled alternatives. In our Lignacite blocks, we also use recycled wood particles in our blocks’ composition for more eco-friendly concrete products.
There are also options to reduce the energy used during the manufacturing process. In our new Brandon factory, we have installed heavily insulated kilns to reduce heating needs, while efficient motors keep electricity usage down. In addition, we have fixed solar panels to the plant to provide renewable energy and reduce our carbon emissions.
As heavy objects, the transportation of concrete blocks is another important consideration when weighing up their environmental friendliness. At Lignacite, we are currently investigating switching to hydrogen fuel, which may become more widespread after the government’s pledge to end new fossil-fueled HGVs by 2034.
Efficient journey planning helps to reduce emissions too. We are already reaping the benefits of this and have boosted our delivery efficiency by 58.9% in just two years (from 2020 to 2022).
On our sites, we have also switched to HVO fuel (hydrotreated vegetable oil) for our plant vehicles. This fuel has 90% of the emissions of standard white diesel.
When weighing up how environmentally friendly concrete blocks are, it’s also important to consider the end of their lifecycle. All of our old concrete blocks are recyclable and can be used as aggregates in hardcore or piling mats at the demolition or construction site.
Are concrete hollow blocks eco-friendly?
Concrete hollow blocks may be considered to be eco-friendly because they can help to bolster a building’s thermal efficiency.
Hollow concrete blocks have empty spaces within their structure, which creates a natural barrier and enhances insulation properties. As such, hollow concrete blocks may help buildings to regulate indoor temperatures effectively.
During colder months, the trapped air within the hollow spaces acts as an insulating layer. This reduces heat loss and minimises the need for artificial heating. When it is hotter, their thermal mass absorbs unwanted heat before releasing it at night, which means air conditioning is less necessary.
Is concrete more environmentally friendly than steel?
Determining whether concrete is more environmentally friendly than steel is not straightforward. At the moment, it’s fair to say that the jury is out.
Production of both steel and concrete is energy-intensive, with both needing high temperatures to reach in their final form. These high temperatures are usually created through the burning of fossil fuels.
Both construction materials need virgin materials too. While steel is highly recyclable, and it is estimated that more than 85% of steel is recycled at the end of its life around the world, demand is so high that raw materials are still required. Concrete also needs raw materials, although it can use recycled aggregates such as pulverised fuel ash in its composition to reduce its embodied carbon.
Indeed, it is estimated that substituting cement with 30% ash can cut CO2 emissions in concrete manufacture by 20%. Concrete can be recycled too. BRE’s Green Guide estimates that 50% of concrete is crushed and recycled and 40% is downcycled (for use in roads, for example).
Both industries are also experimenting with renewable energy and other low-carbon solutions for more sustainable business. Steel manufacturers are trialling hydrogen power and electrolysis, while concrete plants have been making use of solar power. Additionally, there is some promising research going into cement alternatives.
In our own new factory at Brandon, we are using solar power for some of our electricity supply, while more efficient motors and extra-insulated kilns have helped to reduce our energy consumption and improve sustainability.
One distinct advantage that concrete has over steel is that concrete structures can benefit from its thermal mass. Concrete blocks absorb heat during the day before releasing it from the building overnight, reducing the need for artificial heating and cooling.
You can find out more about how the concrete industry is adapting to net zero targets and more sustainable construction in our article.
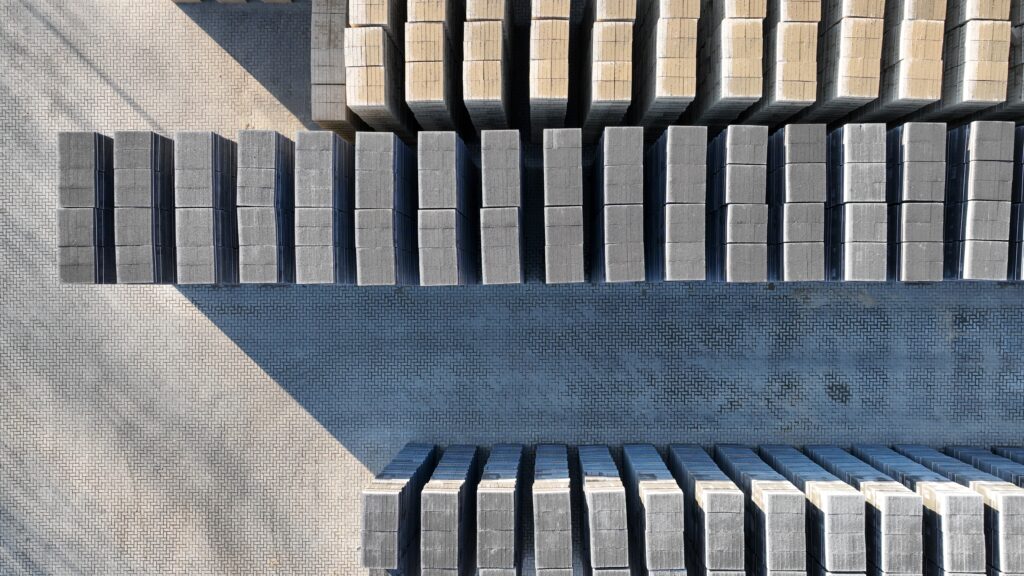
Can concrete be environmentally friendly?
While concrete has a sizable carbon footprint, there is plenty of innovation going into reducing the impact of its constituent parts, including cement.
Cement is a key material to target because it is an important ingredient of traditional concrete. The cement industry produces around 633kg of CO2 for every tonne of cement produced. However, work is well underway on this. Since 1990 the UK cement and concrete industry has reduced the carbon it emits by more than half.
Here’s a quick look at some of the building materials that are being researched for more sustainable blocks.
Hemp in concrete
Hemp, mixed with water and lime, can be used to create green concrete that has excellent thermal performance, strong carbon sequestration properties, and is fully recyclable at the end of its life. Other concrete sustainability benefits include that as a fast-growing plant, it removes more carbon from the atmosphere than it emits during production and application. This makes it an excellent low-carbon concrete solution.
Plastic waste in concrete
Plastic waste is a readily available material that can be used in concrete to increase its green credentials. By doing so, not only is a source of landfill waste recycled, but it adds extra sound and thermal insulation to the concrete mix.
Human waste in concrete
It may sound unsavoury, but research into the use of human waste to make sustainable concrete is ongoing. Bricks are typically made of clay or concrete, but researchers have found that bricks with up to 25% ‘bio solids’ in their composition performed well in strength tests. Their more porous nature also means that the bio-solid bricks are good for thermal insulation.
Micro-silica in concrete
Micro-silica is often a by-product of industrial manufacturing (the production of ferrosilicon and metallic silicon). When added to concrete, it can improve strength and durability, as well as protect reinforcements and embedments from corrosive agents. This makes it a promising proposition for the construction industry.
Coffee in concrete
Researchers have been testing the results of adding processed coffee grounds into concrete to make it stronger. Early investigations have suggested that their addition can increase strength by nearly 30%. The inclusion of coffee grounds also means that less sand can be used while food waste is reduced, creating more sustainable concrete and a smaller environmental footprint.
What is the lifespan of concrete blocks?
When it comes to concrete life expectancy, blocks can range from 100 to 150 years.
Due to their durability and resistance to weathering, concrete blocks can withstand the test of time, making them a reliable choice for various construction applications.
Of course, factors such as the quality of materials used, proper installation and maintenance practices can influence the longevity of a concrete block structure. With routine care and occasional repairs, concrete blocks can maintain their structural integrity, offering a lasting and dependable foundation for buildings, walls and other construction and infrastructure projects.
Find the right block for your project
Need to find the right concrete block for your next construction project? Talk to our knowledgeable team and we can help you to find the perfect fit.