The Building Blocks of Sustainability:
A Case Study
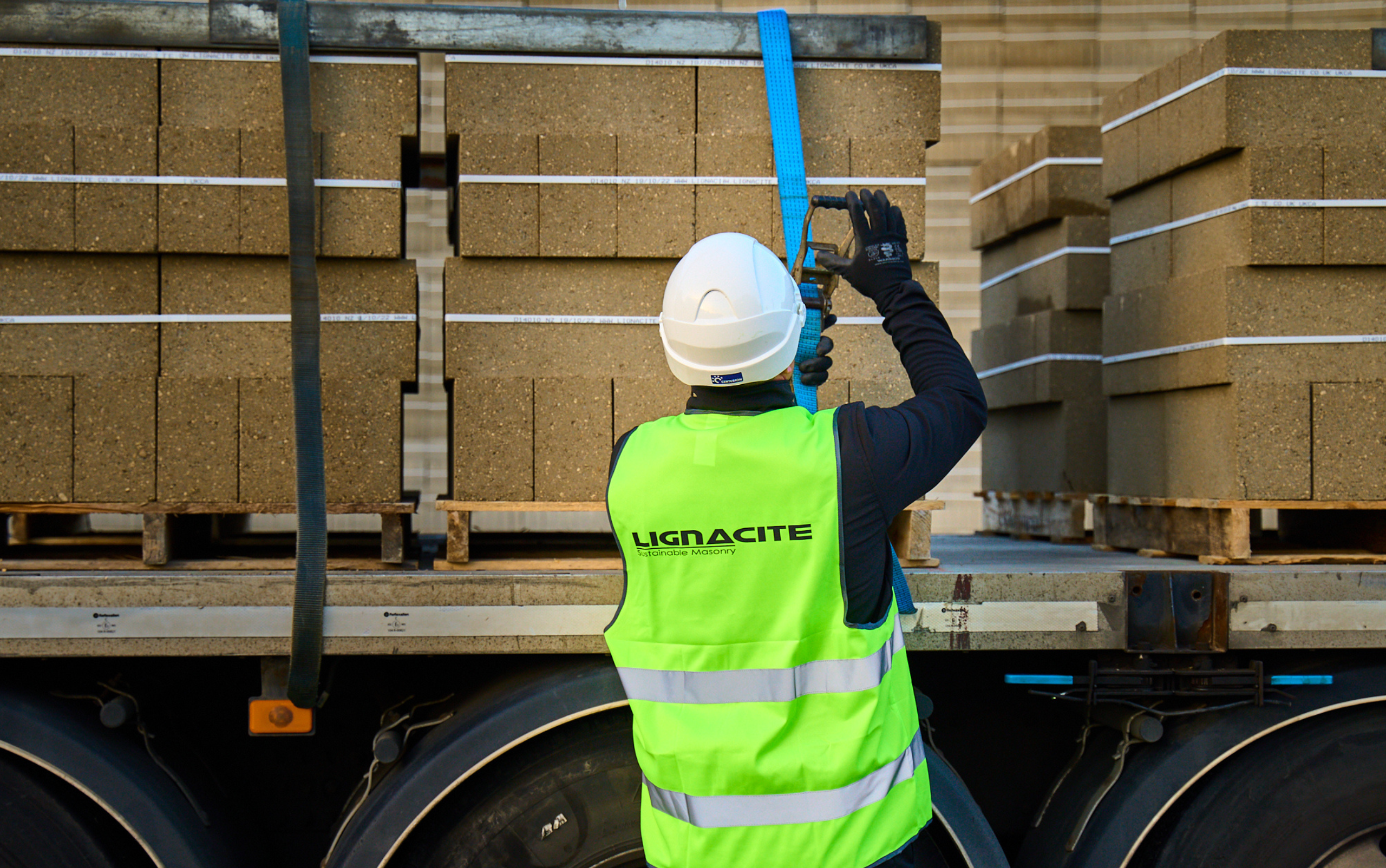
Climate change is one of the most pressing challenges of our time. Influenced by a wide range of factors, including atmospheric composition, solar radiation and ocean currents, the climate is undoubtedly a complex system. However, human activities, such as the burning of fossil fuels, are significant drivers of current environmental damage.
Construction, including the concrete and cement industry, is just one of many human activities adding to this change. According to the Mineral Products Association (MPA), concrete and cement account for 1.5% of the UK’s carbon dioxide emissions. In 2018, these emissions stood at 7.3 million tonnes.
10% of the UK’s carbon dioxide emissions are directly linked with construction activities (UK Green Building Council).
Reducing emissions and reaching net zero is a must for anyone in this sector. In 2012, we therefore made a commitment to a Sustainable Strategy for Masonry, which Lignacite began to implement by achieving certification to ISO 14001, the international standard for environmental management.
As a signatory of the British Precast Charter, we also committed to annual audits to ensure that environmental KPIs are met.
But we knew that this wasn’t enough. We have therefore taken these commitments even further by pledging to reach net zero by 2030, a full 20 years before the government’s deadline.
To do this, we set out to:
- Promote environmental awareness throughout the organisation
- Reduce energy use and choose low-carbon aggregates
- Increase the use of raw materials from sustainable sources
- Switch to low-carbon energy sources where practicable
- Reduce waste through recycling
- Reduce water consumption wherever possible
- Control and reduce air emissions
- Recover, recycle and reuse waste emissions where possible.
The following case study outlines how we have moved along the path to net zero over the last five years and our achievements in reducing, reusing and recycling so far.
REDUCE: TAKING CONTROL OF OUR CONSUMPTION
One important way to take control of our carbon emissions is to manage our use of energy. Manufacturing is a high-energy undertaking, so tackling our consumption and finding ways to reduce it is an absolute necessity.
We therefore set an initial target to reduce our energy use in production by 1% year-on-year against the 2012 baseline of 22.3kWh (kilowatt hour) per tonne. This has now been updated to a more ambitious target of 5% of the previous year’s usage (kWh/m2 ).
Powering up our sites
In 2015, we began tackling the amount of electricity used by our base in Brandon by installing photovoltaic panels at our factory, which now provide 12% of our total electricity at this site.
The lights in our production facilities were also replaced with LEDs, which are activated by motion to cut waste. Efficiency has been increased too, with the amount of electricity needed for block production dropping. For instance, in 2020, 1.04kWh of electricity was used to create each square metre of product.
In 2022, this stood at just 0.77kWh.
Efficiencies for our natural gas use have been found thanks to new monitoring systems installed around our sites. In 2022, just 0.05kWh of natural gas was used for production per metre squared, down from 0.08kWh in 2020.
We also turned our attention to our use of liquid petroleum gas (LPG), which was primarily used to dry the finished blocks. In 2018, LPG was providing 0.40kWh/m2 to our business because the heaters were running around the clock. However, by 2022, a strategy to put the heating on only as needed reduced our use to zero. This is a remarkable achievement considering that in 2020, 484,503kWh was being provided by this energy source.
This is because we recognised that the blocks’ exothermic reaction was already producing a lot of heat. We therefore capitalised on this and used this heat in the kilns to dry the blocks, rather than relying on another source.
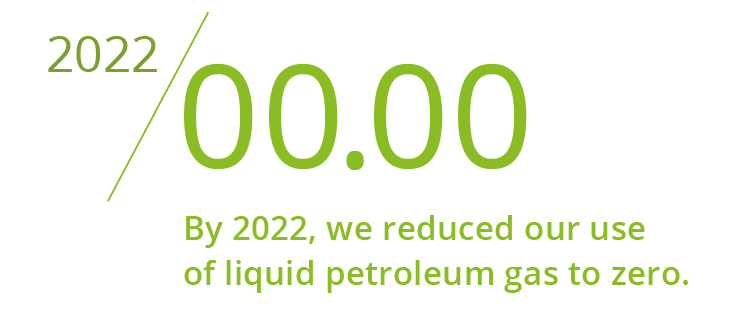
A factory for the future
At our new factory at Brandon, efficiency and sustainability have been part of the design from the very beginning.
Power factor correction ensures that electricity is used efficiently, while light is supplied to the factory floor via a low-energy system. Some of this power is provided by solar panels attached to the factory’s roof.
When it comes to machinery, more efficient inverters have been installed to power more than 90% of our motors. Mixers have been reduced in size to mitigate the risk of dumped loads, and they are run by twin motors to keep energy use to a minimum. With regards to curing, the mix enters heavily insulated chambers, which stay warmer for longer as a result.
Fuelling change
Transport is the largest contributor of carbon emissions in the UK, with approximately 24% of all emissions being produced from this source every year. Construction relies heavily on transport, including industrial plant vehicles. Around 90% of these vehicles are fuelled by diesel.
At Lignacite, our business is heavily reliant upon transportation. As a FORS Gold fleet, we are committed to continually improving our efficiency and environmental awareness, so we began to target our energy use in this area by finding ways to improve the efficiencies of our HGV deliveries to customers. This included improving our calculations and carrying out more detailed route planning to increase the volume of blocks we could deliver per kilometre.
These actions generated excellent results. In 2022, we reduced our total distance travelled by 12.1% from 1,018,698km to 894,940km. At the same time, we increased the total volume of blocks delivered from 2,006,792m2 to 2,797,912m2. This means we boosted our delivery efficiency by an impressive 58.9% in just two years.
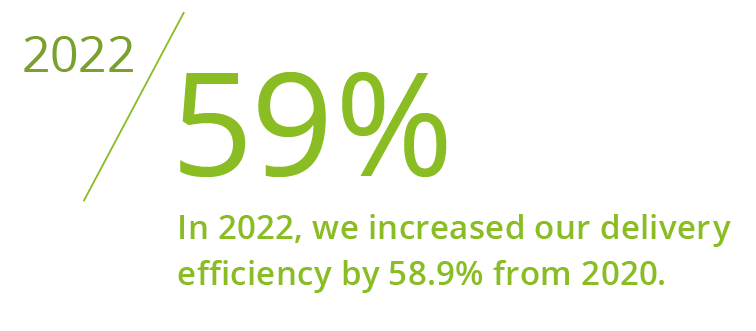
We also set about tackling the emissions produced by our plant vehicles. After the government limited the use of red diesel in April 2022, we took the opportunity to search for a more sustainable alternative.
After extensive research, we chose hydrotreated vegetable oil (HVO). Collected from 100% sustainable sources, this fuel produces 90% less carbon emissions than standard white diesel. It is also beneficial in that it needs no retrofitting or replacement technologies to be added to a vehicle, which
again helps to reduce the impact on the environment.
By the end of March 2023, all 25 of our plant vehicles were switched to this innovative fuel, which will save us 440 tonnes of carbon every year.
A double sign-on system will also help us to keep a close eye on consumption so that we can identify ways to reduce it going forward.
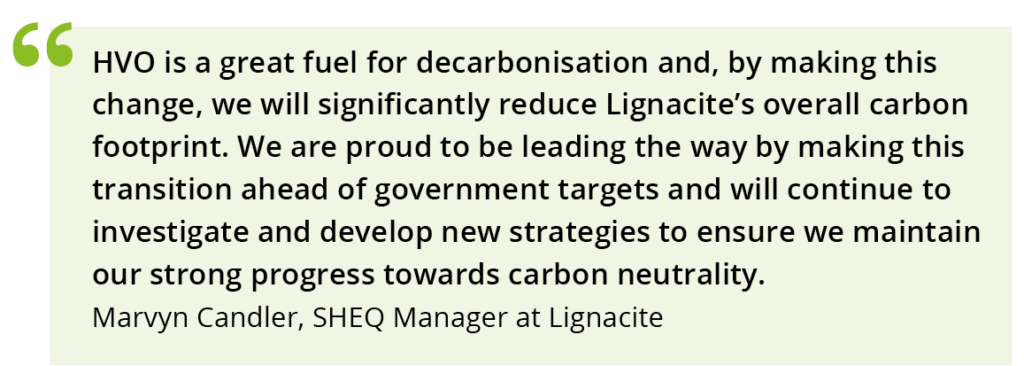
Sustainable success
Our overall success at reducing energy use can be seen below.
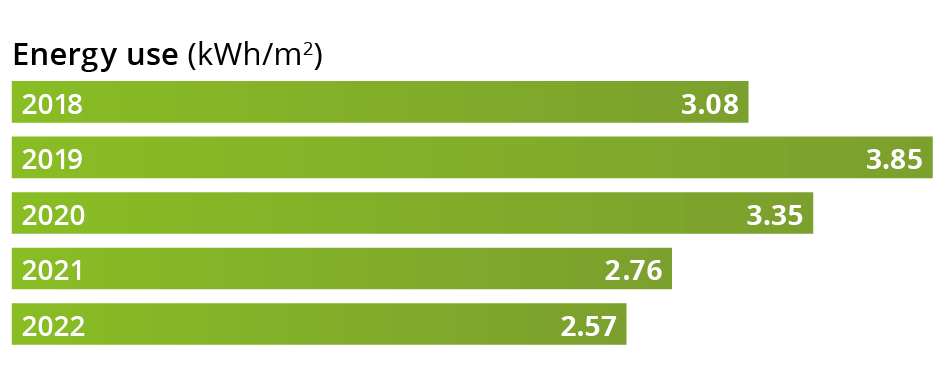
Going forward, our energy management system (certified to ISO 50001) will help us to monitor and improve energy usage even further. This management system has introduced a formal review into our timetable, which occurs twice a year. These reviews will discuss the results of daily energy monitoring, which is being recorded in real time by smart meters. This will enable us to cut consumption and uncover new ways in which renewable sources can be implemented.
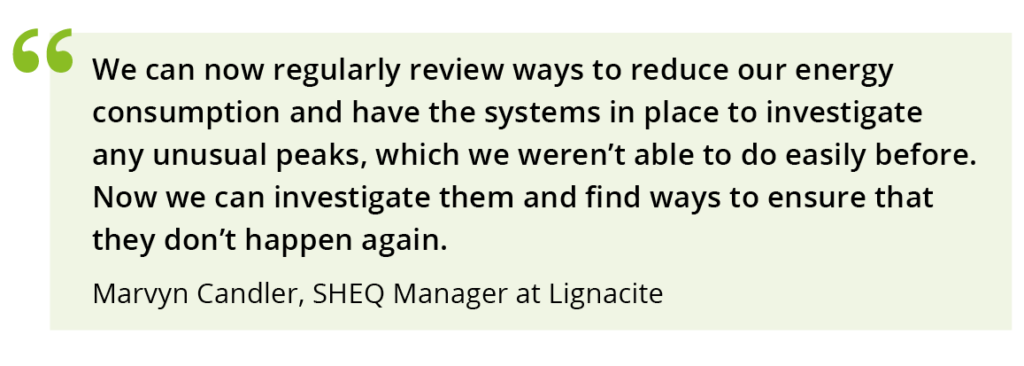
REDUCE: TAKING RESPONSIBILITY
Responsible raw resources
In order to create our products, we must have access to raw materials. But this has not meant that we can absolve ourselves of the responsibility for how and where these materials are acquired.
Our materials are sourced according to BES 6001, the standard for responsible sourcing in construction. By applying this standard to our procurement process, we ensure that our masonry products are responsibly sourced to an independently verified level. This addresses all of the social, economic and environmental impacts across the supply chain. Traceability is an absolute must to make sure that all requirements are being met.
The efficiency of our raw material procurement is further enhanced by our quality management system, which is certified to ISO 9001 (a standard we have maintained since 1990). This means that strict quality controls apply to our supply chains and waste is limited to maintain efficiency.
Paper cuts
We are reducing the consumption of raw materials at Lignacite by moving our business over to a paperless system.
We no longer send paper invoices, and our delivery drivers are kitted out with digital delivery notes and job tickets. We have also switched our archives to a digital format, reducing our reliance on paper and ensuring that our information is kept in a secure and sustainable way.
Designing the future
As a manufacturer, we must consider the role our products play in the built environment’s overall sustainability.
We therefore played an instrumental role in creating Environmental Performance Declarations (EPDs) for aggregate blocks on behalf of the British Precast Concrete Federation. These certificates provide those in the construction sector with transparent and easily comparable information about
the environmental impact of blocks throughout their lifecycle.
But we wanted to give architects and specifiers a clearer idea of the exact sustainable performance of our own blocks, too.
As a result, work is currently underway on the production of independently verified EPDs for our entire range, which will provide our customers with accurate information for each and every block.
REUSE, RECYCLE: LIMITING WASTE
Recycled and reused materials
While using fewer resources is an important part of the equation when developing more sustainable practices, the reduction of resource and manufacturing waste at the other end of the process should not be overlooked. Reusing and recycling materials not only improves efficiency, but it also reduces the burden on landfill.
At Lignacite, we have had an ethos of recycling from our very earliest days. The original Lignacite blocks created in 1947 contained recycled wood particles, an aggregate that continues to be a signature feature of our flagship Lignacite range.
Our blocks have also made use of crushed glass and furnace bottom ash as sustainable aggregates.
Recycling our waste
Thanks to our improved focus on measuring what we use, it has been possible to identify more situations in which we can send our waste for recycling. In 2022, we recycled 17,638 tonnes of our own waste in this way, a huge increase from the 7,718 tonnes that were sent for recycling in 2020.
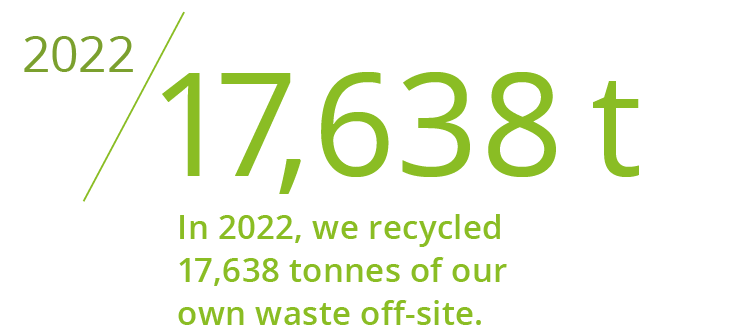
Waste at the end of our products’ lifecycles is reduced by the fact that all of our blocks are fully recyclable. They can be used as aggregates in hardcore or piling mats at the demolition or construction site.
LOOKING AHEAD
A net zero future
Over the last five years, we have made great progress towards our goal of net zero. Sustainability has been fully integrated into our business operations, and with our energy management system now up and running, along with greater tools for monitoring, we expect to continue making excellent strides towards our goal.
Our current target is ambitious: to reduce carbon levels by 0.7kg/m2 of production in Brandon and 0.25kg/m2 in Nazeing. So far, we are on track to meet this target, which is reviewed annually to ensure that we continue to push ourselves to do better. However, we know we need to do more to maintain this, which is why we are focused on researching new solutions to further reduce our carbon footprint.
Projects that are underway include the exploration of alternative recycled and sustainable materials for block production. If successful, these will further enhance our eco-credentials and sustainable offering.
Now that our plant fleet is operating on more sustainable fuel, our focus has also switched to our HGV vehicles. With transport being such a major part of our business, finding a green solution to this would make a huge difference to our underlying carbon footprint. We are therefore keenly researching the developing infrastructure for hydrogen fuel in the UK. Bio LPG could be another alternative coming to power Lignacite in the future.
In the meantime, we will continue to expand our provision of solar power to both our sites and keep a close eye on
consumption via our daily monitoring systems.
Becoming a net zero manufacturer in such a carbon-heavy industry was never going to be easy. But this report shows that improvement is possible and achievable, and with every step we take, we get closer to our 2030 goal.
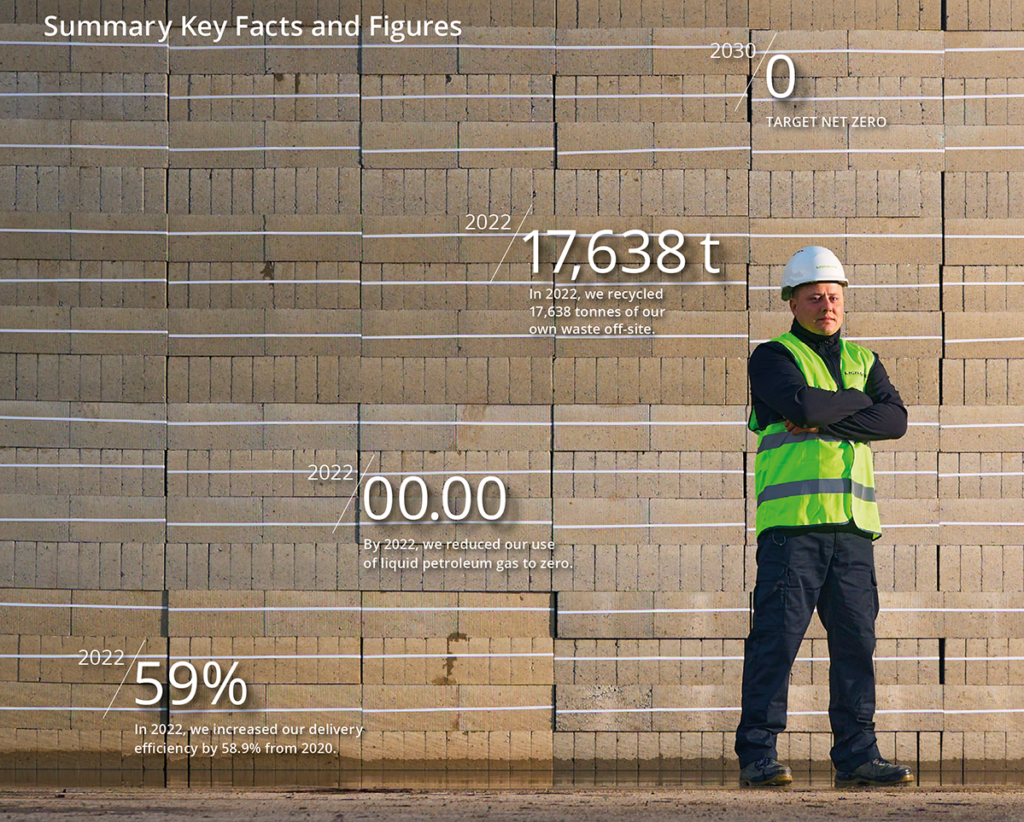
Download the case study here:
For further information or to make an order enquiry, please contact:
Brandon Sales
E: brandonsales@lignacite.co.uk
T: 01842 810678
Nazeing Sales
E: nazeingsales@lignacite.co.uk
T: 01992 464441
To learn more about our sustainability ambitions and initiatives, visit lignacite.co.uk/sustainability