Articles
The Building Blocks to Net Zero
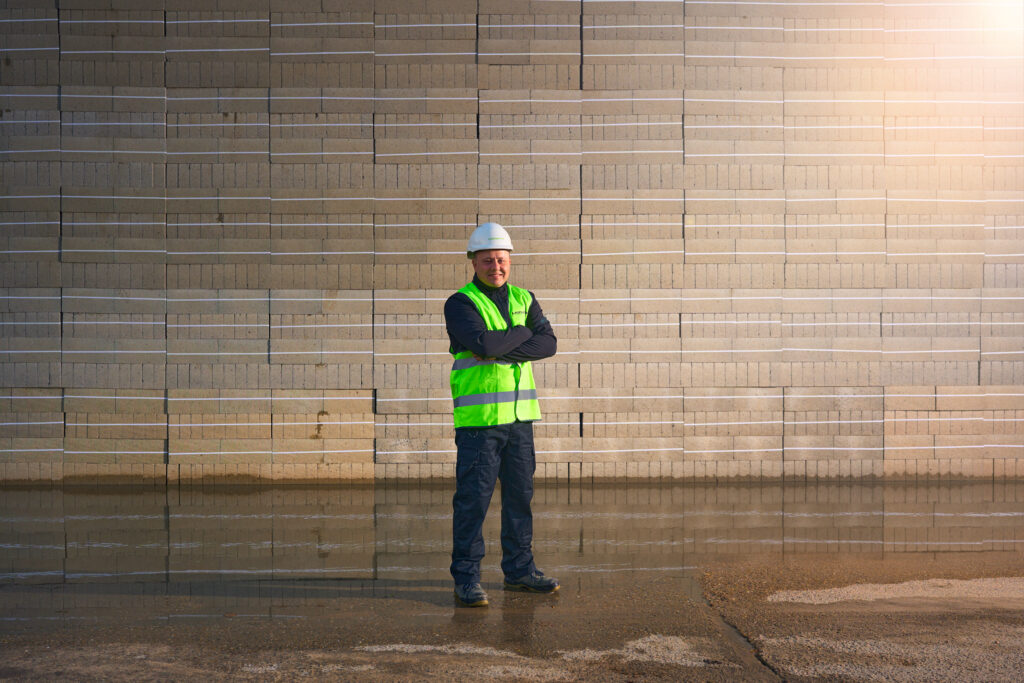
Posted by Nick Franks
How can the concrete masonry industry adapt in the race to net zero?
By Miles Hogg, National Specification Manager, Lignacite
The need to become carbon neutral and contribute towards the UK’s net zero target is the latest challenge in a long list that has faced the concrete masonry sector in the last few years. The industry has consistently risen to meet these challenges, but how can the sector really embrace stronger sustainability?
An introduction to the industry’s carbon emissions
Concrete masonry – a description for all types of concrete blocks and bricks – is the most widely used wall material in the UK. Masonry solutions in new housing account for around 80% of the housing market[1], but its use is not just confined to this sector. There is also strong demand in the commercial, educational, leisure and retail sectors.
According to the Mineral Products Association (MPA)[2], concrete and cement currently account for around 1.5% of the UK’s carbon dioxide emissions. Early action by the industry means that this is about five times lower than the global average (7%), but this doesn’t mean that the job is done and dusted.
For instance, the MPA has also reported that the UK’s carbon dioxide emissions from concrete and cement stood at 7.3 million tonnes in 2018.
Reducing CO2 emissions in concrete masonry
The government’s ‘Net Zero Strategy: Build Back Greener’ has set out policies and proposals for decarbonising all sectors of the UK economy to meet the nation’s net zero target by 2050.
The concrete masonry sector, part of the wider precast and concrete industry, has therefore adopted the UK Concrete and Cement Industry’s ‘Roadmap to Beyond Net Zero.’
Although roadmaps are vital in setting out the vision, it will be up to individual sectors and businesses to create their own micro strategies. So, what are some of the practical steps that can be taken by the concrete masonry sector to reach its net zero carbon targets?
Cement carbon-saving
Compared to other industries, the concrete masonry sector uses relatively little cement. However, for every tonne of cement produced, around 622 kilograms of CO2 is emitted[3], and it remains an important contributor to the masonry’s carbon footprint. The cement industry is therefore reforming by embracing improvements in process, alternative fuels and carbon capture, usage and storage. Investigation into new supplementary cementitious materials is also underway, which will further help to reduce the carbon footprint of the cement used.
Aggregates
Aggregates are the major component of concrete blocks and bricks by volume and are inherently low-carbon products. Most are locally sourced, naturally occurring materials that require little processing. In addition to primary aggregates, suitable materials for use in concrete include air-cooled blast-furnace slag, crushed concrete aggregate (CCA), and manufactured and lightweight aggregates. By-products from the china clay industry, sometimes referred to as stent, can also be used.
Increased efficiencies in the manufacturing process
Carbon reduction will be supported by investment in more efficient production processes and projects to decarbonise the factories. The latter includes investing in renewable technology.
A modern concrete block plant using renewable energy solar panels to improve its carbon footprint.
Greener transport
Generally, concrete blocks and bricks are delivered by road. Investment in new fleet vehicles and reduced road transport miles will therefore help to lower carbon emissions. This endeavour will be aided by the government’s pledge to phase out new fossil-fuel-powered heavy goods vehicles by 2035[4].
Taking advantage of carbonation
Key properties of masonry can also contribute to ‘beyond net zero’ during the operation lifetime of buildings.
Over time, CO2 in the atmosphere reacts with the calcium oxide in concrete to form calcium carbonate, a process called carbonation. This is recognised in the UK’s accounting of greenhouse gases. In practical terms, this means that concrete products absorb CO2 from the atmosphere during their lifetime of 100-150 years.
Over this period, carbonation will result in the reabsorption of around a third of the CO2 emitted when making cement[5], significantly reducing the whole-life CO2 footprint of both the cement and the concrete for which it is used. In lower-strength concrete, such as blocks and bricks, carbonation is more rapid during its service life, as CO2 permeates the material more easily.
Some masonry blocks such as Lignacite are also produced using a proportion of graded wood particles, which further increases its carbon sequestration throughout its lifetime.
Thermal insulation
The insulation properties of lightweight and aerated concrete products are not currently factored into lifecycle assessments. Once they are, they will enhance the net-negative potential.
Thermal mass
Thermal mass is a concept in building design that describes how the mass of the building can prevent internal temperature fluctuations. This is typically achieved through its ability to absorb unwanted heat during the day and then release it at night with the help of ventilation from cool night air.
Concrete masonry can provide a very useful level of thermal mass and, if appropriately designed, can help to eliminate the CO2 emissions that would otherwise be used in the mechanical heating and cooling of buildings.
To sum up…
Overall, there is much to do and consider for net zero to be achieved by 2050. However, the process for carbon reduction in the concrete masonry sector is well underway and there is huge carbon-saving potential, all of which bodes well for the future.
[1] National Housing Building Council
[2] The Mineral Products Association – UK Concrete and Cement Industry Roadmap to Beyond Net Zero)
[3] Cement: How its carbon footprint can be reduced - Construction News
[4] Gov.uk – “UK confirms pledge for zero-emission HGVs by 2040 and unveils new chargepoint design”